Il cemento è la seconda commodity più utilizzata al mondo, dopo l’acqua. Secondo l’ultimo Cement 2022 Report, la produzione globale di cemento nell’ultimo anno è stata di 4,37 miliardi di tonnellate, per un consumo di 4,27 miliardi di tonnellate (+6% rispetto all’anno precedente), da cui deriva una produzione di 14 miliardi di metri cubi di calcestruzzo. Un mercato fiorente (circa 330 miliardi di dollari nel 2021, che arriverà a 444 miliardi nel 2027), per un materiale ancora indispensabile al settore delle costruzioni, ma per il quale il mondo paga un prezzo importate: la produzione del cemento è responsabile fino al 7% delle emissioni globali di CO2.
Per fornire una tonnellata di cemento, il processo di cottura a 1.400 °C produce circa una tonnellata di CO2. Questo sistema, rimasto inalterato da quando il cemento è stato prodotto per la prima volta, oltre 200 anni fa, è responsabile del 70% delle emissioni, mentre il restante 30% proviene dall’energia utilizzata per tenere accesi i forni di lavorazione. E se a questi dati si aggiungono quelli relativi al trasporto, alle fasi di costruzione e allo smaltimento post-demolizione, è evidente il paradosso: l’insostenibilità conclamata di un materiale che resta però indispensabile, in quanto “sostiene” la quasi totalità di quel che si costruisce nel mondo.
Utopia?
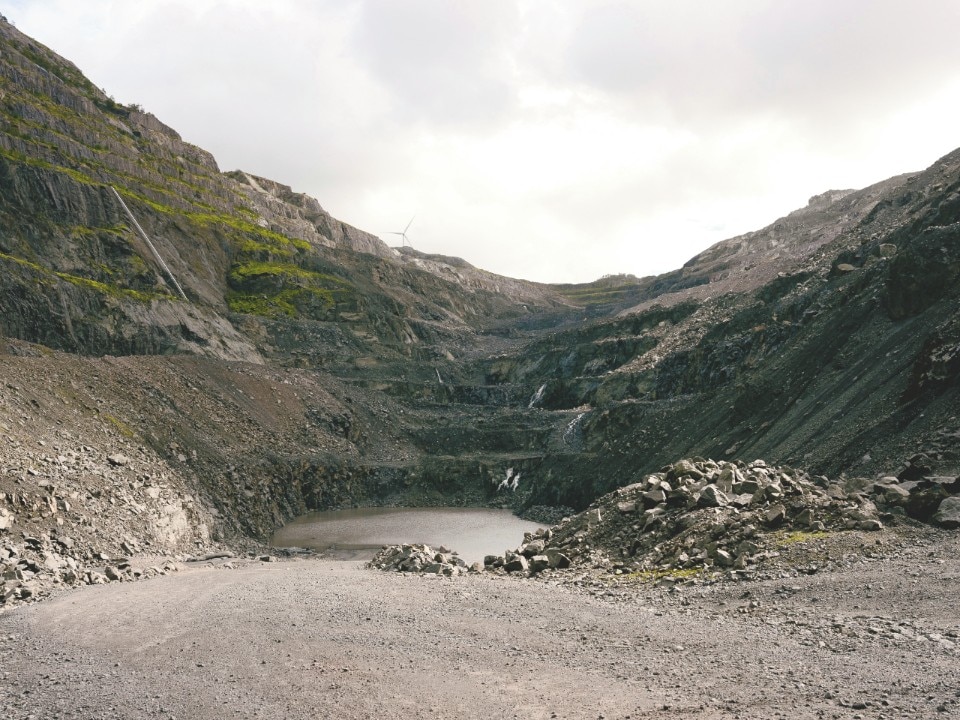
Il galoppare delle normative sempre più stringenti rispetto alle emissioni, e le altrettanto stringenti politiche Esg che orientano la finanza industriale, unite a una sensibilità crescente su questi temi, spingono l’industria dei materiali nell’unica direzione praticabile: non tanto un costruire meno, quanto un costruire meglio, puntando sulla tecnologia e sulla ricerca per sviluppare materiali capaci di garantire le stesse prestazioni e funzioni infrastrutturali, o magari migliori, con un minor impatto ambientale. Utopia?
Qualche esperimento interessante, facendo un giro d’orizzonte tra poli universitari, consorzi di ricerca e centri di ricerca e sviluppo dei big del settore, lo si incontra. Piccoli segnali, ad alto contenuto tecnologico, di una possibile rivoluzione futura. Un esempio interessante e per certi versi visionario proviene dal centro di ricerca sui materiali della facoltà di ingegneria dell’Università del Colorado-Boulder, dove è in corso una sperimentazione sul calcestruzzo a emissioni zero. Il principio sul quale si basa lo studio è l’integrale sostituzione della componente cementizia con il calcare derivato dalle alghe, che lo producono naturalmente durante il processo di fotosintesi.
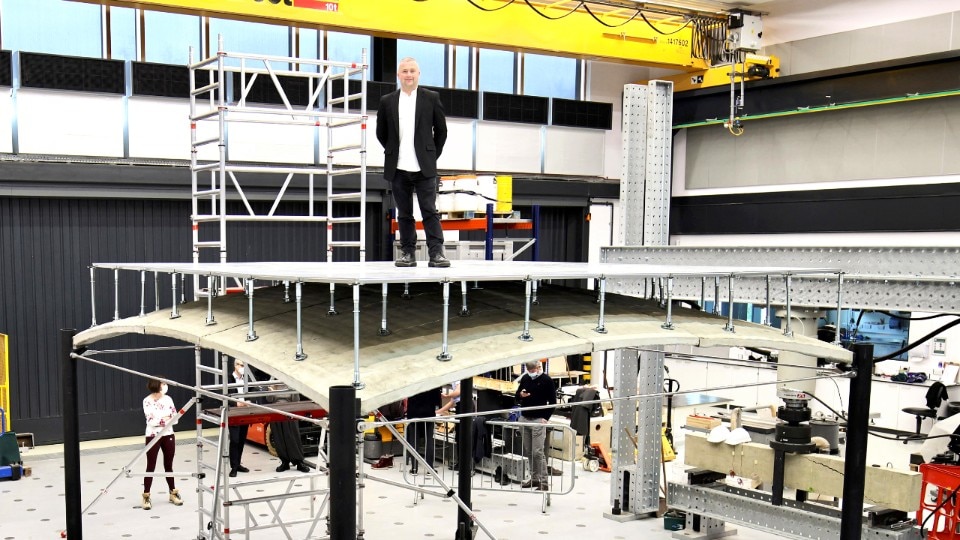
Secondo i ricercatori, il prodotto finale è un materiale carbon neutral, in quanto l’anidride carbonica rilasciata durante le fasi di produzione del nuovo calcestruzzo è pari a quella prelevata dall’atmosfera durante il processo di crescita dell’alga stessa. Il team di lavoro ha ricevuto un sovvenzionamento di 3,2 milioni di dollari dall’US Department of Energy per proseguire la propria ricerca e si tratta senza dubbio di una soluzione “circolare” interessantissima, ma che funziona per ora solo all’interno di un laboratorio universitario, deve fare i conti poi con i grandi numeri della domanda di materiale: per soddisfare l’intero fabbisogno di calcestruzzo degli Stati Uniti, sarebbe necessaria una superficie 4mila chilometri quadrati di stagni preposti alla coltivazione intensiva delle alghe. Non semplice.
Guarda sempre all’ambito dei biomateriali la ricerca dello studio londinese Newtab 22, che sta lavorando alla sperimentazione di un nuovo prodotto simile al cemento realizzato a partire dalle conchiglie di scarto dell’industria alimentare, le quali macinate e combinate con miscele di leganti naturali, mimano in modo soddisfacente il cemento riproducendone il contenuto di carbonato di calce, fondamentale alla costituzione del calcestruzzo. Per quanto la sperimentazione presenti degli indubbi tratti di interesse, anche in questo caso la scalabilità dell’idea rispetto ai quantitativi di domanda globale frena un po’ gli entusiasmi: la produzione di questo cemento naturale dipende da un approvvigionamento di risorse che, per quanto naturali, non sono rinnovabili e rappresentano dunque una fonte esauribile e non quantitativamente significativa a livello di scarto. I materiali da costruzione immessi sul mercato dell’edilizia pubblica necessitano di brevetti e certificazioni internazionali che difficilmente possono essere conferiti a materiale che di fatto sottenda, una volta esaurita l’esigua fonte di scarto alimentare, la depauperazione della flora marina.
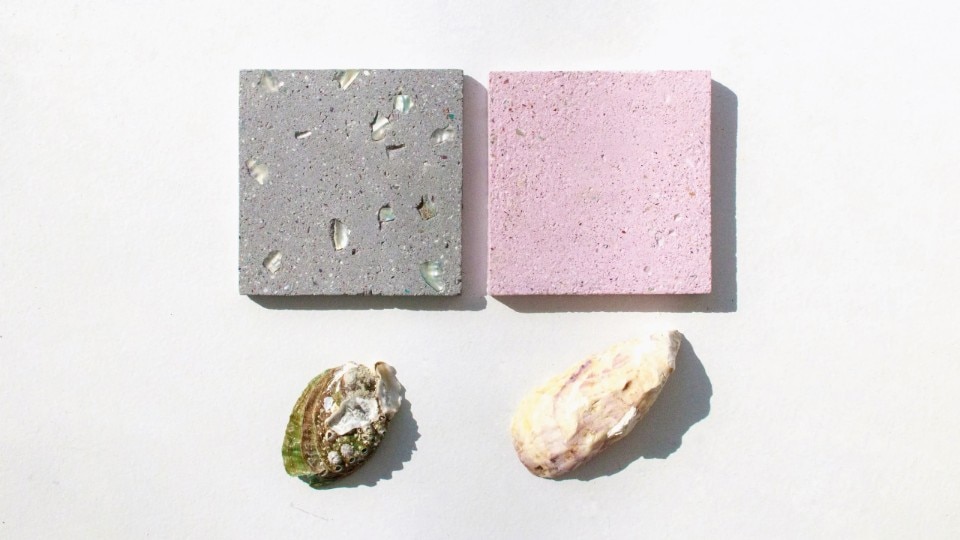
Un approccio più conservativo ma altrettanto interessante è quello proposto dai ricercatori delle Università di Bath, Cambridge e Dundee, all’interno del progetto Acorn (Automatic Concrete Construction), il cui principio verte sulla capacità del cemento di potersi reinventare non tanto nella propria composizione chimica quanto in quella strutturale. Beneficiando infatti delle elevate prestazioni ormai raggiunte dalla progettazione parametrica e computazionale, è possibile efficientare il volume di materiale strutturalmente necessario.
Il team multidisciplinare che lavora al progetto ha realizzato all’interno del Dipartimento di Ingegneria civile dell’Università di Cambridge una volta a conchiglia di strato molto sottile, che sfruttando al meglio la resistenza a compressione del materiale, permette un risparmio del 75% di calcestruzzo rispetto a una tradizionale struttura piana, che richiede spessori considerevoli data la limitata resistenza del calcestruzzo alla flessione. In una struttura a volta, il peso scorre lungo l’arco e non vi è necessità di rinforzi, ma solamente di uno strato di pannelli piani standard per pavimenti sopraelevati. Un’ipotesi vincente per la sua semplicità, che potrebbe rivoluzionare anche il mondo della progettazione delle infrastrutture.