Cement is the world’s no. 2 commodity by weight after water. According to the Cement 2022 Report, global production of cement in 2022 was 4.37 billion tons, of which 4.27 billion tons were consumed (+6% over 2021), producing 14 billion cubic metres of concrete. A booming market (roughly $ 330 billion in 2021 and projected to grow to 444 billion cubic metres in 2027) for a material that is still indispensable for the construction industry, but one that costs the world a pretty penny: cement production contributes up to 7% of global CO2 emissions. To produce one ton of cement, the material is heated to 1,400°C, which releases close to a ton of CO2.
This process, which has remained substantially unchanged since cement was first produced over 200 years ago, is the source of 70% of emissions, while the remaining 30% comes from the energy used to keep the processing kilns in operation. And if we add to this the CO2 produced by transporting, constructing, and post-demolition disposal, the paradox is clear: the obvious unsustainability of a material that is unfortunately indispensable since it “sustains” nearly everything we build in the world.
Utopia?
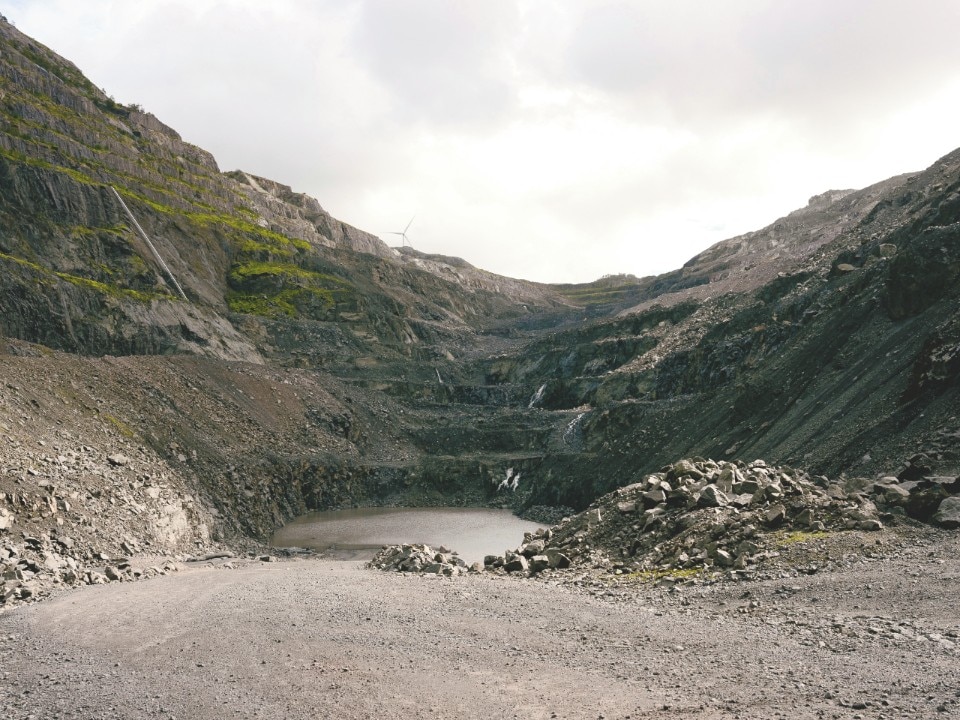
A spate of increasingly strict emissions regulations and equally stringent ESG policies guiding industrial finance, coupled with growing awareness and concern about these issues, drive the raw materials industry in the only feasible direction: not so much building less as building better, investing in technology and research to develop materials that can provide the same (or even better) performance and functions in infrastructure with a lower environmental impact. A utopia?
Scanning the horizon of university research efforts, research consortia, and R&D centres of the big players, we observe a number of interesting experiments, small but highly technological signals of a possible future revolution. An interesting – and in some ways visionary – example is found at the Materials Research Center of the Department of Engineering of the University of Colorado-Boulder, where experimentation is underway on zero-emission concrete. The principle behind the study is the total replacement of the cement component with calcium carbonate produced by algae, a natural by-product of photosynthesis.
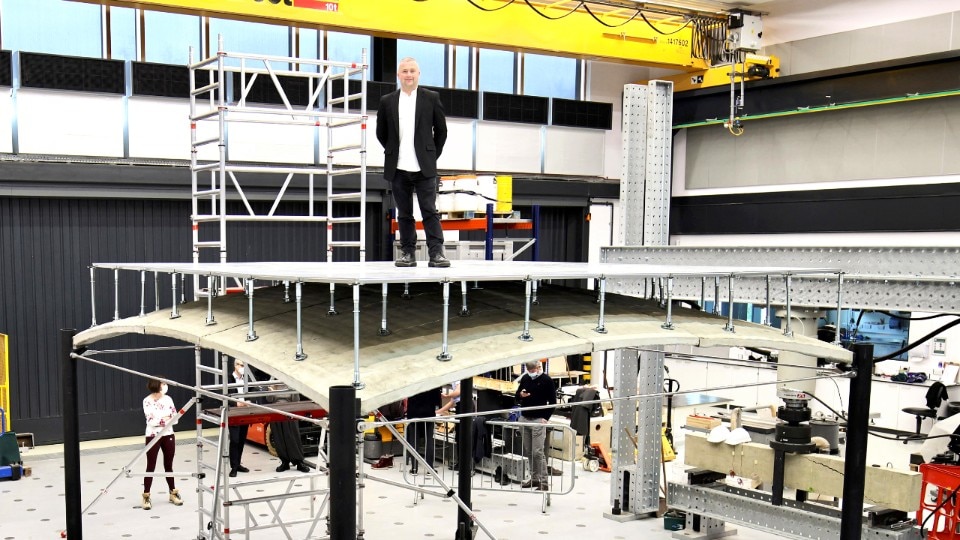
According to the researchers, the resulting material is carbon neutral, in that the carbon dioxide released during the production of the new cement is equal to that removed from the atmosphere during the growth process of the algae. The research team has received a grant of 3.2 million dollars from the U.S. Department of Energy to continue its research. Of course, while it is unquestionably a very interesting “circular” solution, it is one thing if it works in a university laboratory, it is another thing to get it to work on a real-world scale: to meet demand for cement in the United States, four thousand square kilometres of wetlands dedicated exclusively to intensive algae production would be necessary. No simple matter.
Another outfit focusing on the use of biomaterials is Newtab 22 in London, which is experimenting with a new product similar to cement produced using waste mollusc shells from the food industry. Ground up and mixed with natural binders, they produce a satisfactory alternative to cement, supplying the calcium carbonate that is necessary for the production of concrete. While the effort is certainly interesting, scalability is again an issue, with the magnitude of global demand tending to dampen enthusiasm. The production of this natural cement depends on supplies of resources which, while natural, are not renewable at the needed scale: the food industry produces only limited amounts of this waste. Construction materials on the public market require licenses and international certification that are unlikely to be granted to materials that—once the available waste materials have been consumed—would cause the depletion of marine fauna.
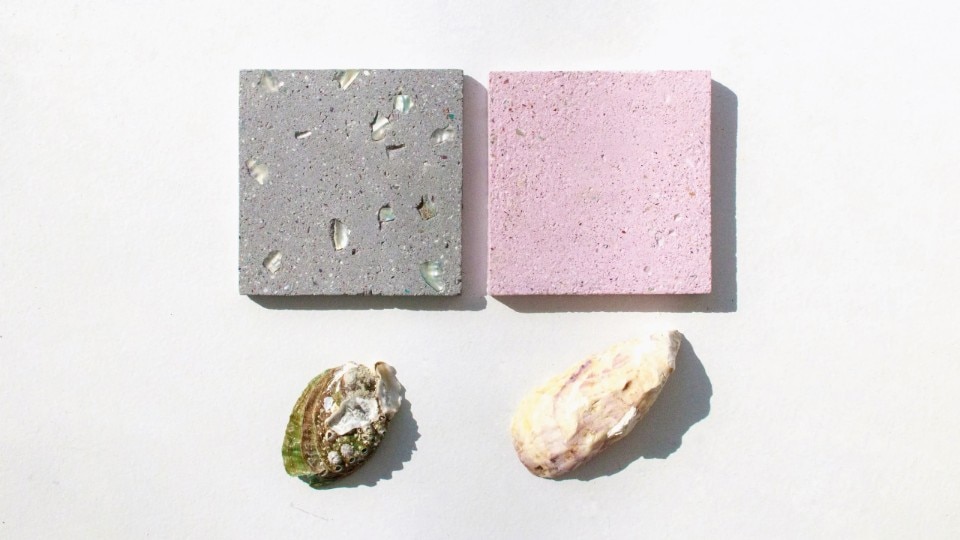
A more conservative but equally interesting approach has been proposed by researchers at the universities of Bath, Cambridge, and Dundee as part of the Automatic Concrete Construction (ACORN) project. The principle here is the possibility of reworking cement not so much in its chemical composition as in its structure. Taking advantage of the high performance now achieved in parametric and computational design, it is possible to optimize the volume of material that is structurally necessary.
The multidisciplinary team at the Department of Civil Engineering of the University of Cambridge has built a spiral vault using a very thin layer of cement. Exploiting the resistance of the material to compression, they were able to reduce the amount of concrete by 75% with respect to a traditional flat structure, which requires significant slab thickness to overcome concrete’s limited resistance to bending. In a vaulted structure, the weight is transmitted along the arc and there is no need for reinforcement, only a layer of standard flat raised-flooring panels. The idea is powerful for its simplicity and may have the potential to revolutionize infrastructure design.