Questo articolo è stato pubblicato in origine su Domus 1051, novembre 2020.
In pochi mesi, la pandemia di Covid-19 ha avuto un impatto drammatico sulle società e le economie di tutto il mondo. Le risposte alla crisi hanno rivelato forti differenze in termini di resilienza economica, nei contratti sociali tra le persone e i loro Governi e nella reattività delle istituzioni, in particolare dei sistemi sanitari. Alcuni Paesi si sono scoperti più preparati a coordinare un intervento e a sfruttare un’ampia gamma di competenze presenti nel proprio ecosistema di ospedali, università, laboratori di analisi e imprese manifatturiere.
Durante la prima ondata dell’epidemia globale, in Paesi come il Regno Unito e l’Italia si è manifestata la carenza di ventilatori e dispositivi di protezione di base. La rapida crescita della domanda globale ha inoltre evidenziato la necessità di risposte senza precedenti. I Governi hanno impostato diverse iniziative orientate alla risoluzione di questi problemi, in base alle quali è stato chiesto agli attori pubblici e privati in tutto l’ecosistema nazionale d’identificare e coordinare una risposta. Sebbene siano stati raggiunti importanti traguardi, i percorsi di progettazione e produzione hanno presentato problematiche significative e inaspettate.
Allo scoppio della pandemia, nel Regno Unito il Sistema Sanitario Nazionale (NHS) disponeva solo di 8.000 ventilatori, mentre i modelli epidemiologici suggerivano la necessità di 30.000 apparecchi di lì a poche settimane. Il 14 marzo scorso, il governo britannico ha lanciato il consorzio Ventilator Challenge UK, che riuniva importanti aziende industriali, tecnologiche e ingegneristiche del campo aerospaziale, automobilistico e medico. Le aziende di questi settori fanno affidamento su piattaforme tecnologiche simili, catene di approvvigionamento flessibili costituite da fornitori altamente specializzati e capacità di progettazione coerente per tutti i sistemi di prodotto. Tali aziende lavorano con gli ecosistemi tanto quanto con i prodotti.
L’High Value Manufacturing Catapult ha assunto un ruolo di coordinamento, in particolare nello studio di una gamma di opzioni di progettazione e di specifiche per un sistema di ventilazione a produzione rapida sviluppato dai medici e dall’Agenzia di regolamentazione dei medicinali e dei prodotti sanitari. Date le complesse interdipendenze tra soluzioni progettuali, disponibilità delle tecnologie e difficoltà nella fabbricazione in tutta la catena d’innovazione e produzione, in tempi normali questo processo d’indagine avrebbe richiesto mesi, o addirittura anni.
In un momento di crisi, il rapido aumento delle soluzioni progettuali presenta sfide ancora maggiori
In un momento di crisi, il rapido aumento delle soluzioni di progettazione presenta sfide ancora maggiori. In lotta contro il tempo, lavorando a progetti paralleli e concorrenti, diverse aziende (spesso con capacità di progettazione specialistica non medica) hanno collaborato per sviluppare un prototipo nell’arco di poche settimane. Mentre molte aziende hanno tentato di sviluppare soluzioni di design completamente nuove, un gruppo si è basato su architetture di prodotto e soluzioni di design già testate ed efficaci. Molti di coloro che hanno deciso di “partire da zero” hanno sottovalutato il fatto che la sicurezza del dispositivo non è automaticamente parte del progetto. Dipende piuttosto da come il dispositivo è prodotto, dalla gestione della qualità e da quanto l’aspetto innovativo del design del prodotto sia adeguato a soddisfare le esigenze cliniche. Guidare questo processo utilizzando scorciatoie intelligenti e intuizioni condivise, evitando supposizioni generalizzate che offuscano l’inventiva, è un delicato esercizio di equilibrio. L’approccio tradizionale tramite bandi e concorsi non favorisce la stretta collaborazione richiesta in tali situazioni (generando invece concorrenza), e l’attuale posizione dell’agenzia di Finanziamento dell’innovazione tende a non essere abbastanza vicina a questi fronti in rapido movimento per apprendere e guidare l’operazione. Allo stesso modo, un nuovo virus rappresenta un contesto in continua evoluzione. In aprile sono emerse nuove esigenze cliniche che hanno reso inappropriate alcune delle soluzioni progettuali iniziali. I pazienti di Covid-19 tendono a soffrire di un rapido accumulo di liquidi nei polmoni, quindi i ventilatori devono consentire un drenaggio frequente. In alcuni casi, è stato necessario rispedire in fabbrica un certo numero di ventilatori medicali per effettuare delle modifiche, con conseguenti ritardi. La produzione si è poi incentrato in ultima analisi su due soluzioni progettuali: il dispositivo Penlon Prima ESO 2 e il paraPAC plus. Il consorzio è riuscito ad aumentare la capacità combinata della Penlon and Smiths passando da 50-60 ventilatori alla settimana a 100-200 al giorno. Il 5 luglio il consorzio si è sciolto dopo avere consegnato al NHS 13.347 ventilatori.
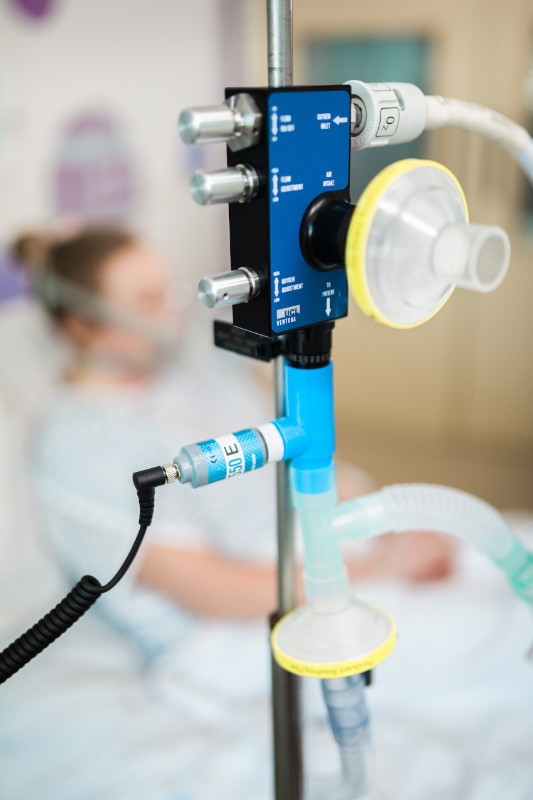
In Italia, alla fine di marzo, una risposta progettuale alternativa alla carenza di ventilatori è arrivata dal basso: i medici del Policlinico Sant’Orsola di Bologna sono riusciti a raddoppiare lo stock esistente progettando un circuito attraverso il quale si potesse utilizzare un unico dispositivo per ventilare due persone contemporaneamente. Sarebbe rimasta semplicemente un’idea se l’ecosistema industriale dell’Emilia Romagna non fosse stato in grado di produrre in soli tre giorni un prototipo funzionante di “doppio ventilatore”.
Il distretto biomedicale di Mirandola è un cluster d’imprese specializzate nella produzione di dispositivi medici: dagli apparecchi monouso alle complesse macchine per emodialisi. Tutti fanno parte di sistemi di prodotto critici, insieme con apparati di flusso e fluidici, sensori e software integrato, valvole e sistemi di filtrazione. Data la complessità della loro architettura, le capacità d’integrazione e la modularizzazione della progettazione del prodotto sono fondamentali.
Un approccio multidisciplinare, basato sull’ingegneria e su forme più articolate di capacità progettuale, potrebbe avere sbloccato una serie più ricca di soluzioni
La carenza di ventilatori ha portato anche a soluzioni progettuali innovative lungo diverse linee terapeutiche, come i dispositivi a pressione positiva continua (CPAP) sempre più usati.
A differenza dei ventilatori, le macchine CPAP erogano ossigeno tramite una maschera e non richiedono l’intubazione. Un team dell’University College London (UCL) ha lanciato a marzo l’iniziativa UCL-Ventura, dedicata agli ausili respiratori. Lavorando in collaborazione con Mercedes AMG High Performance Powertrains e facendo affidamento sull’accesso diretto ai medici dell’ospedale UCL, UCL-Ventura ha portato alla produzione di 10.000 dispositivi in un mese e oltre 1.900 licenze in 105 Paesi. Il progetto originale del 1992 prevedeva un dispositivo puramente meccanico controllato semplicemente da valvole rotanti per variare la concentrazione di ossigeno e la portata. Sebbene il prodotto fosse molto più semplice di un ventilatore, il team dell’UCL non sarebbe stato in grado di migliorare il sistema CPAP senza un partner industriale.
Il processo d’ingegneria inversa si è basato sulla progettazione assistita da computer e simulatori di meccanica dei fluidi computazionali, normalmente utilizzati per la progettazione del motore di Formula 1. I miglioramenti del design sono state limitate dalla scarsa disponibilità di materiali di consumo, successivamente prodotti da Intersurgical.
Lo sforzo produttivo ha dovuto anche affrontare problemi d’implementazione, determinati dalla fornitura limitata di ossigeno negli ospedali britannici. Il team di Ventura ha modellato i flussi di ossigeno a ogni piano e area letto dell’ospedale, quindi ha progettato una soluzione integrata prodotto-sistema-terapia.
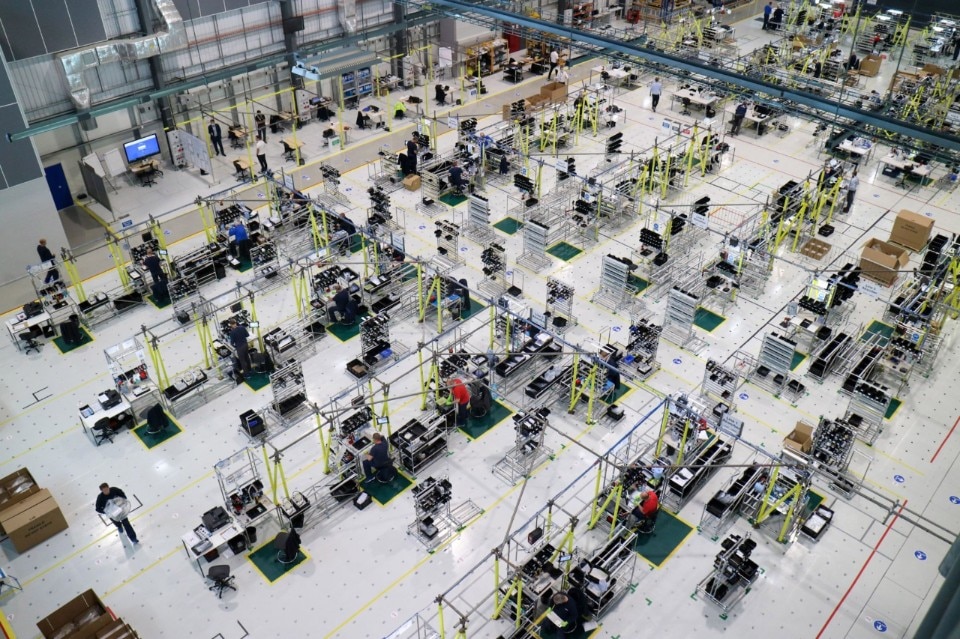
Per i dispositivi di protezione che presentavano un design del prodotto semplice, come le mascherine usa e getta, l’impegno progettuale si è indirizzato soprattutto sullo sviluppo di tecnologie e processi di produzione affidabili e altamente automatizzati, in grado di tenere alti numeri per lunghi periodi. In Italia, per esempio, la carenza di mascherine è stata affrontata da un’azienda leader di macchine per l’imballaggio, la IMA Spa. In questo caso, rispondendo all’appello del governo italiano, l’azienda ha sviluppato una linea di produzione snella e altamente flessibile – IMA Face 400 – in grado di produrre (e confezionare) tra 200 e 400 mascherine al minuto. La progettazione di 25 macchine in grado di soddisfare la domanda nazionale è stata guidata da un’agile task force interna all’azienda, nonché una rete di appaltatori specializzati che hanno saputo fornire componenti nonostante le restrizioni del lockdown. Una catena di approvvigionamento resiliente si è dimostrata fondamentale per trovare le soluzioni più appropriate per la progettazione di processi e sistemi di prodotto.
Several lessons have been learnt from design and manufacturing solutions that emerged during the pandemic
Il contesto di tali tecnologie è accessibile grazie alle diverse discipline di progettazione, come il triumvirato formato da design d’interazione, design di servizi e design strategico. Adottare un approccio multidisciplinare, basandosi sull’ing gneria, ma aggiungendo forme più articolate di capacità progettuale, potrebbe avere sbloccato una serie più ricca di soluzioni diverse. Tali soluzioni potrebbero essere più immediatamente efficaci, più economiche, più veloci da implementare, più facili da usare sia per il personale medico sia per i pazienti, oltre che caratterizzate da una sensibilità alla diversità culturale necessaria in tali contesti. Gli approcci guidati dall’ingegneria generalmente non giungono a toccare questi aspetti. Allo stesso modo, la progettazione strategica farebbe nascere intuizioni più ampie: un esempio è la catena di fornitura just-in-time orientata all’efficienza e le logiche di approvvigionamento sono arrivate a dominare soprattutto l’assistenza sanitaria, in particolare nel Regno Unito. Queste questioni più ampie possono essere affrontate in base alla progettazione e sono fondamentali per costruire una vera resilienza, o almeno per volgere la crisi in positivo. È improbabile, però, che emergano da una Ventilator Challenge guidata dalla High-Value Manufacturing Catapult.
Come spesso accade, un’attenzione troppo superficiale verso scienza, tecnologia e ingegneria sviluppa buchi neri sugli aspetti più ambigui, ma ugualmente produttivi, della cultura, delle regolamentazioni e della politica. Se i ventilatori dovevano essere prodotti, e rapidamente, anche il tema più ampio del perché essi non fossero già disponibili va di certo preso in esame. Non si tratta di un problema ingegneristico, ma può essere affrontato con diverse forme di progettazione e produzione.
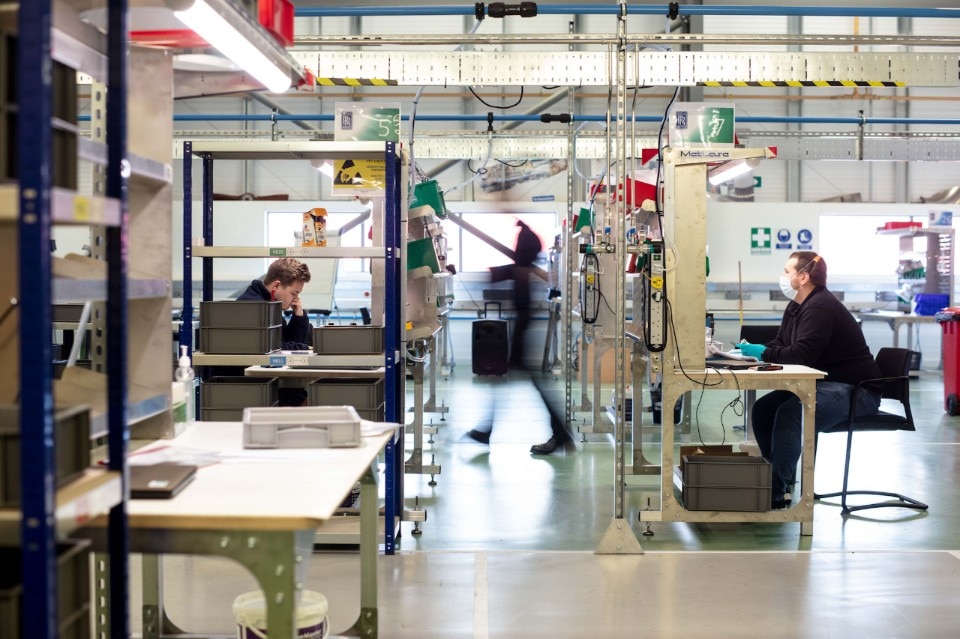
Quelle emerse gli scorsi mesi durante la pandemia ci hanno fornito numerose lezioni. La pandemia ha infine rivelato come lo sviluppo e la diffusione delle capacità di progettazione nei settori sanitari sia al centro dell’ecosistema dell’innovazione, ma anche delle scelte che abbiamo fatto sulle infrastrutture quotidiane che compongono l’assistenza sanitaria. In entrambi i casi, le forme di progettazione possono aiutare a migliorare la resilienza delle società e delle economie in tempi di crisi.
Parte di questa sfida progettuale riguarda soluzioni funzionalmente appropriate e convenienti. Un’ulteriore sfida progettuale riguarda innanzitutto i contesti politici più ampi che favoriscono, o intralciano, tali soluzioni resilienti. Lo sviluppo di questa serie più articolata di capacità progettuali, che va ben oltre l’ingegneria, può generare tecnologie sanitarie sintonizzate sulle persone e sulla specificità locale, permettendoci di gestire le emergenze che oggi ci troviamo ad affrontare, sia a breve sia a lungo termine.
Antonio Andreoni lavora presso l’Institute for Innovation and Public Purpose, University College Londra, Inghilterra.
Dan Hill lavora presso l’Institute for Innovation and Public Purpose and Vinnova, Svezia.