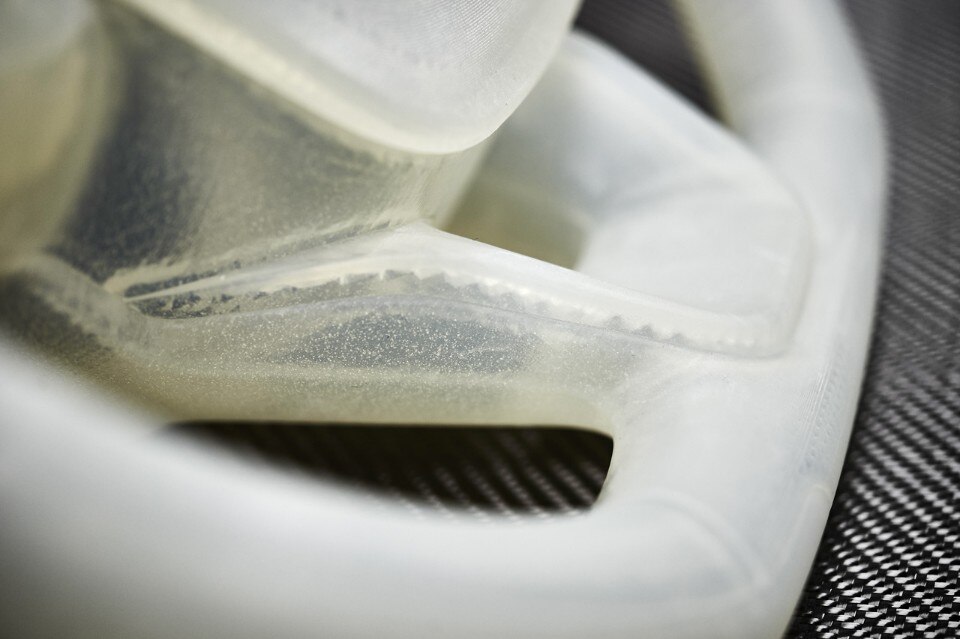
The first step in bringing a design to life is a sketch produced by the design team. Clay modellers then make a scale- and later full-size model of the vehicle to assess proportions and develop the design. In parallel, digital sculptors will create a model using computer-aided design (CAD). The two models are developed together, leveraging the strengths of both disciplines.
While some parts are worked in clay, more complex or detailed items are mostly developed digitally and often 3D printed – this is where the Rapid Prototype team, based at Ford’s European headquarters in Cologne, Germany, comes into play.
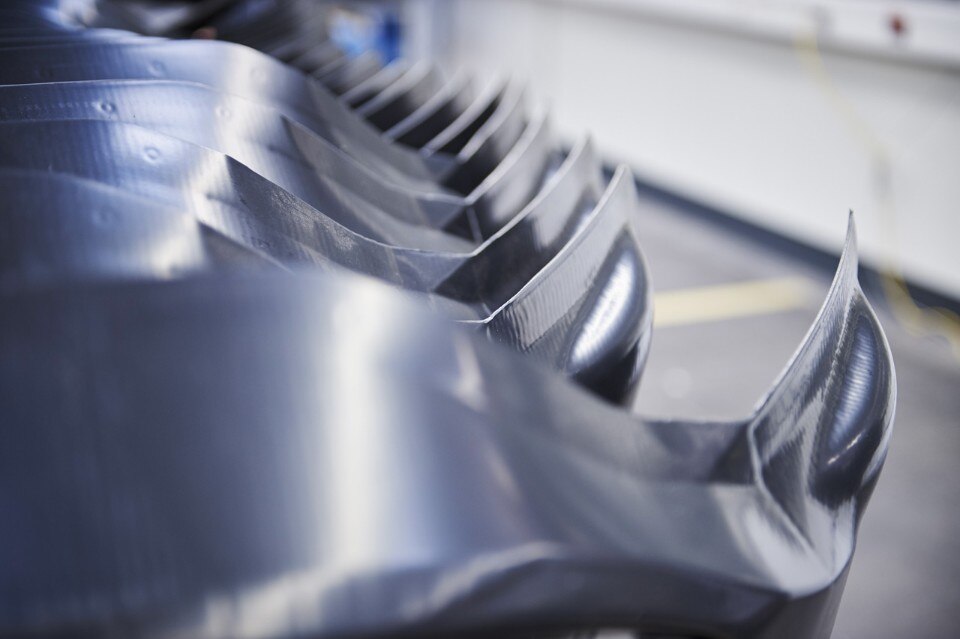
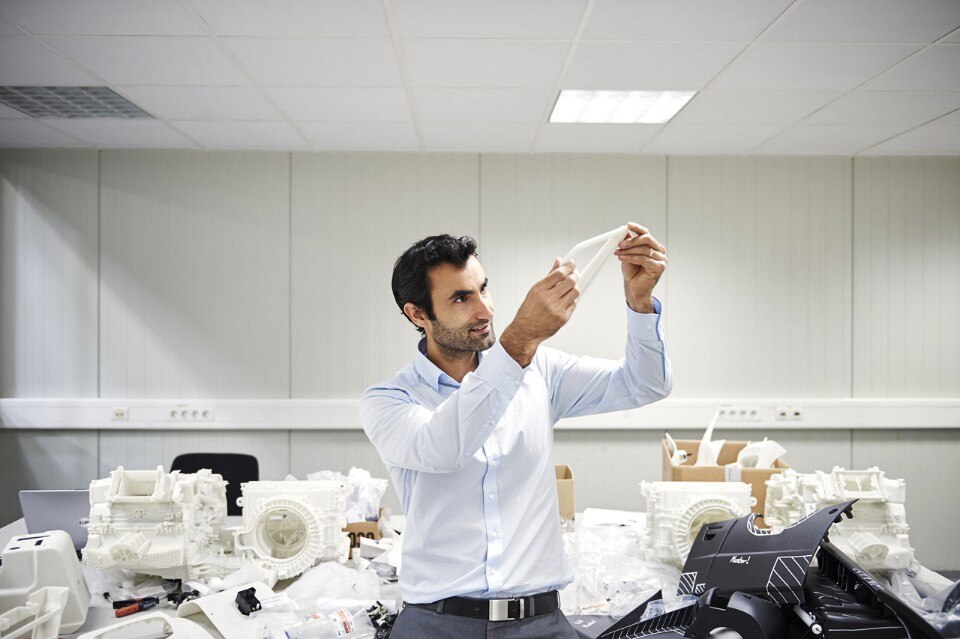
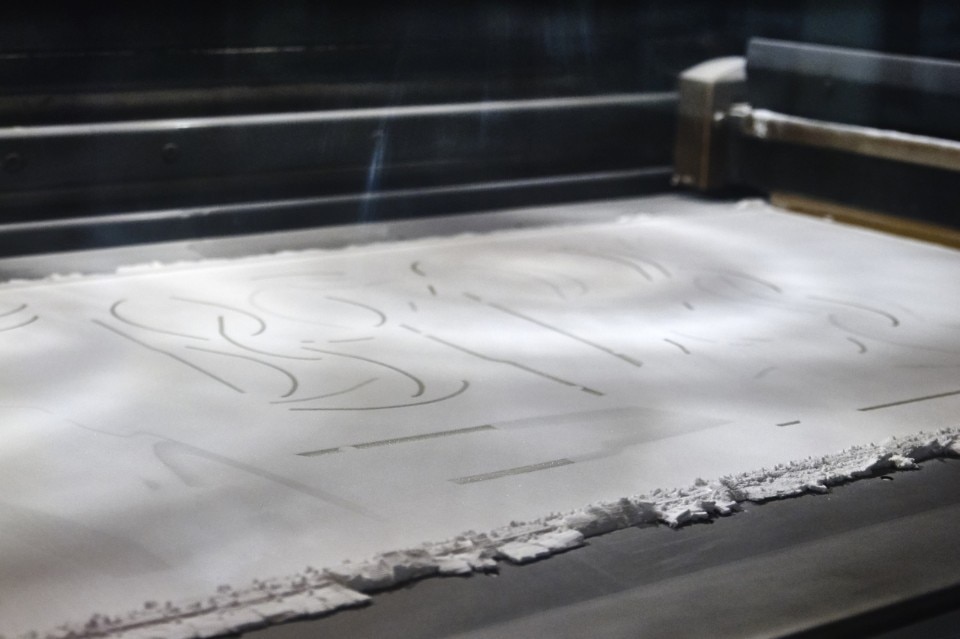

The value of solidity
Riva1920 creates solid wood furniture using certified or reclaimed materials, combining sustainability, high-quality craftsmanship, and timeless design. An Italian excellence focused on durability, transparency, and authenticity.