WATCH THE VIDEO
MT3 is a variation on the theme of the void, a subject Ron Arad already addressed with Driade in 1994 with the Empty Chair project. In that particular case, research into the void involved more sophisticated processes for curving wood. As with this new design, the effort to subtract material required carefully developing the production processes, to adapt them to the requirements of expressing the form. Normally we are used to considering closed forms with an empty, imperceptible inside. Ron Arad instead follows the opposite procedure, tending to empty the forms that are thought of as closed, while pushing the materials’ possible uses to the limit.
Contradicting material
Arad has a vocation for always contradicting the material used to make his objects, for example his series of chairs in stainless steel plate. He managed to work this apparently difficult and hard material in such a way as to make it sensual, soft and organic. One could describe it as an exercise in “wrong-footing” materials. When it came to making this rocking chair (which is part of the MT series, along with a chair and sofa), Arad asked us to try and mould it using rotational technology that could obtain a two-colour material. From a practical point of view, achieving a two-colour material entailed developing a double injection of material, each occurring at different times. Special containers are inserted at the side of the mould that, as soon as the first layer has partly solidified, inject the second material of a different colour.
rotation moulding
Rotational moulding works more or less like this: the mould in die cast aluminium is heated in an oven and rotated continually so that the fluid material (polyethylene in mass coloured powder) is distributed over the whole internal surface. The first layer forms the outside of the piece. Once solidified it affords structure to the chair as well as giving its external colour. Immediately afterwards the droll boxes come into action, which are special devices fixed on the sides of the mould. These function as bulkheads and are programmed to inject a second quantity of material when the mould is semi-cooled. Automatic systems control the whole process, with no manual intervention. The second colour is overlaid on the first, thus creating a new, thin layer. With the rotational technique, the mould is much simpler compared to that used for injection moulding. The second layer of colour has a smooth finish simply because of the rotation’s effect on the material. The outside layer, being in contact with the surface of the mould, instead assumes a rougher texture. This is the difference in quality between the two surfaces and therefore between the different colours.
The development process
During the development phase, there was always a sense of anticipation while waiting for the mould to cool so we could cut the piece. If the material had not been evenly distributed, there would be areas where the outer layer’s colour emerged. Managing to make the internal part uniform was the most complicated operation. It was necessary to distribute the heat over the whole surface of the mould, bringing the most internal areas to the right temperature. In order to perfect the process we had to use masking and special silicon-based materials to reduce the heat in some areas and increase it in others. This careful development of the mould required a long series of trials and tests in order to understand, for example, how the material is distributed according to fluid dynamics, or what quantity of material is necessary to give the structure solidity. It was particularly complicated to find the right masking for the sofa seat that would allow a uniform distribution of the material. The mould also contains profiles that identify the cutting areas in the sides of the chair; a numerically controlled machine with five axes registers any dimensional difference and compensates the variations before finally making the cuts. This compensating is an importantfor resolving the phenomenon of withdrawal, which in the case of rotational moulding is much higher than with injection moulding. Before beginning production, the piece is sent to CATAS, the main italian institute for structural controls, which puts the object through rigorous testing – a bit like crash tests for cars. They evaluate its resistance to static and dynamic loads and check that it complies with European regulations. The MT chair was given an award from CATAS for its resistance.
Taken from a conversation between Francesca Picchi and Sergio Buttiglieri, project manager at Driade
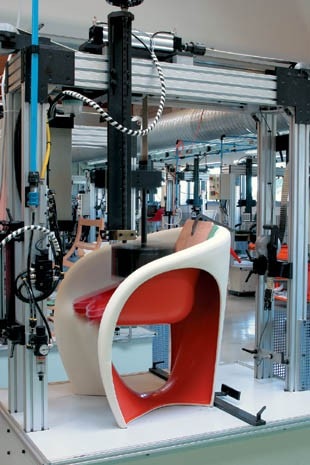







The Mirra 2 combines ergonomics and sustainability
Redesigned by Berlin-based Studio 7.5, the Mirra 2 chair from Herman Miller represents the perfect combination of function and innovation.