The KamerMaker is a shiny silver contraption that sits on the side of a road in North Amsterdam, a few hundred metres from the Central Station and the Ij. A perforated, mirrored, six-metre-high industrial container tilted on its side, it resembles a monolith from outer space, or a menhir from a forgotten age, rooted to the ground since time immemorial. A few plastic helixes hang from its sides, standing still in this particularly grey morning. It is March 2013, and the KamerMaker seems to be waiting.
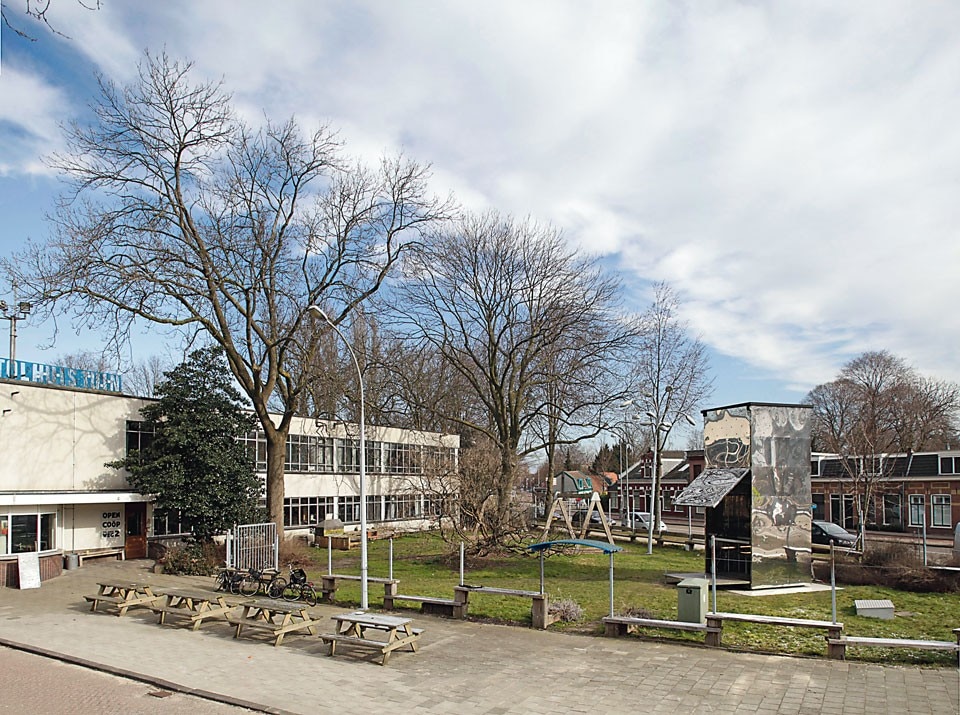
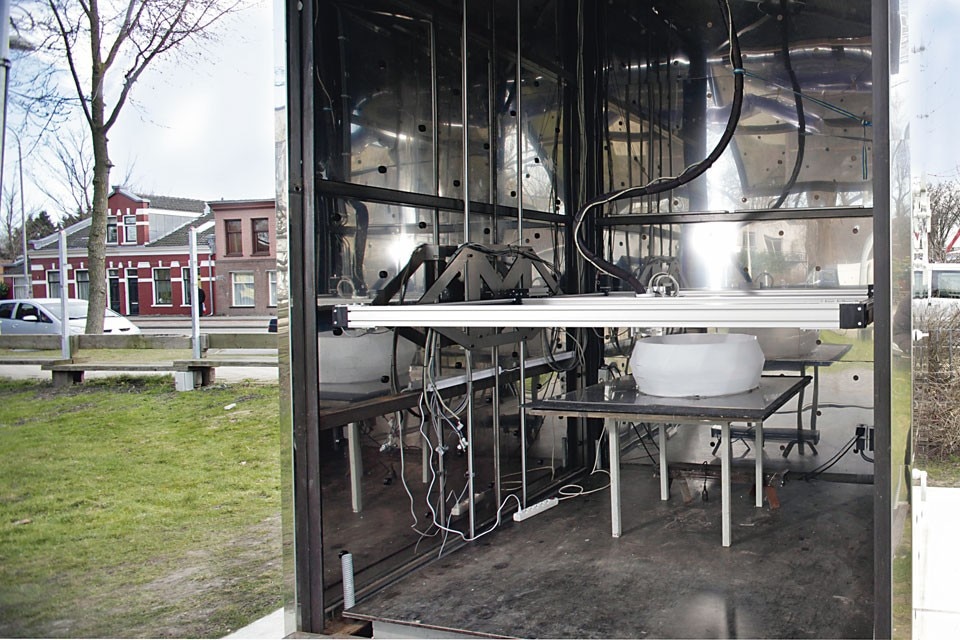
Their 2009 Gecekondu Summerhouse Hotel was an ephemeral 300-sandbag structure that travelled to several locations offering “free lodging in exchange for cultural contribution”. From children’s birthday parties to one-day exhibitions, the Gecekondu Summerhouse Hotel served as a gathering space and an open platform for events—with a frequently updated website as a companion to the physical structure, effectively linking the space’s physical and virtual dimensions. The project attracted the attention of the Architectuurcentrum Amsterdam, and was later deemed the “best architecture project of 2009” by the NRC Handelsblad’s Tracy Metz.

Located on a site formerly belonging to Shell in North Amsterdam — 20 hectares of buildings that were partially demolished in anticipation of new construction which never materialised after the onset of the economic crisis, and currently one of the city’s most dilapidated neighbourhoods — the Open Coop is a collaboration between dus and social engineers Partizan Publik, an open studio where cooks, artists, data analysts and politicians share space with architects and engineers. Here, walls have been torn down, forcing collaboration and interaction between different disciplines.
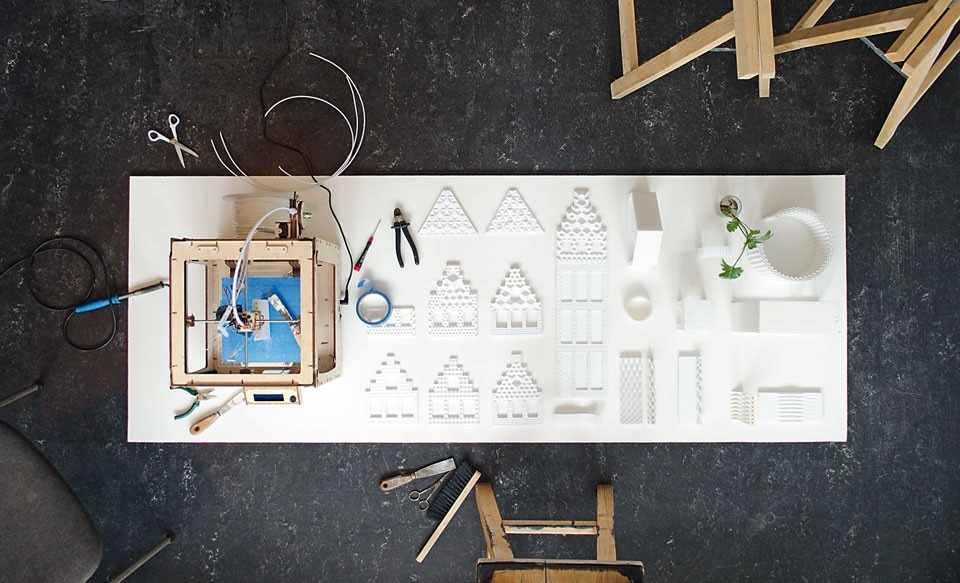
It was in this collaborative context that, in the fall of 2012, the KamerMaker was born. The inauguration of the structure coincided with the city’s innovation and creativity festival PICNIC, and launched the question: what if we 3D-print our own house? “We were already fascinated by 3D printing,” says Heinsman, “and liked this idea of actually having a pavilion that can move around, react to its surroundings and produce something new.” But instead of tracking down investors to kick-start the project, DUS offered a more proactive approach, taking the first steps on their own and waiting for the reactions — which were overwhelmingly positive.
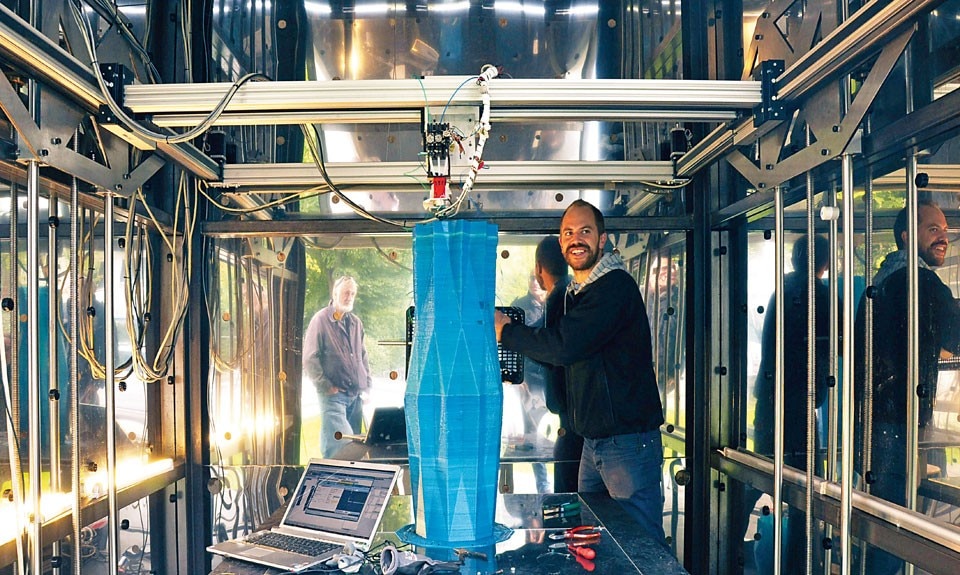
The studio has made use of their now solid relations with diverse partners, from the municipality to construction companies, and is taking the first steps into what may potentially become the synthesis of all the work they have developed so far, creating an experimental research site where multiple stakeholders — including sponsors and community members — are invited to intervene in a co-creation process, where progress is measured and evaluated step by step.
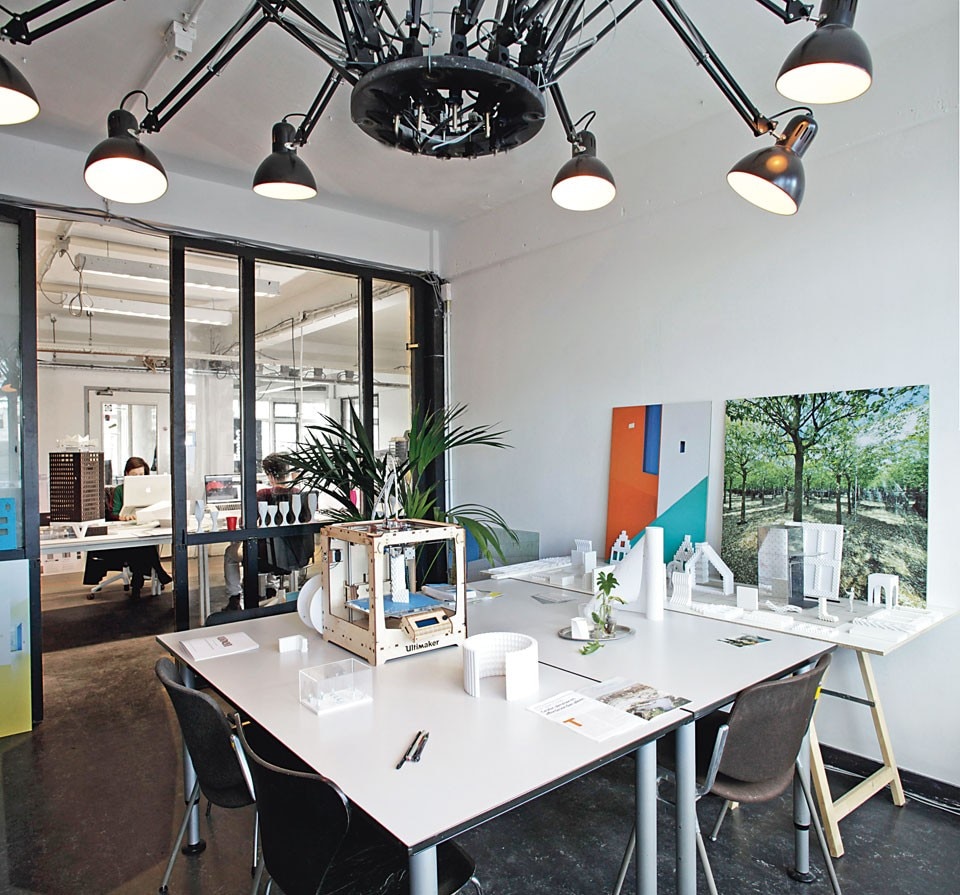
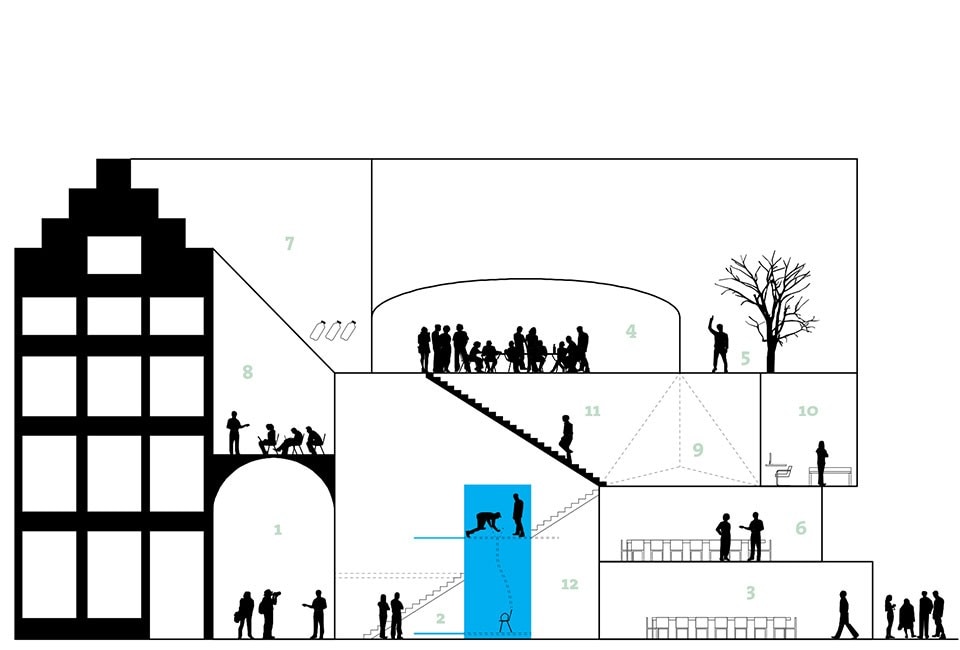
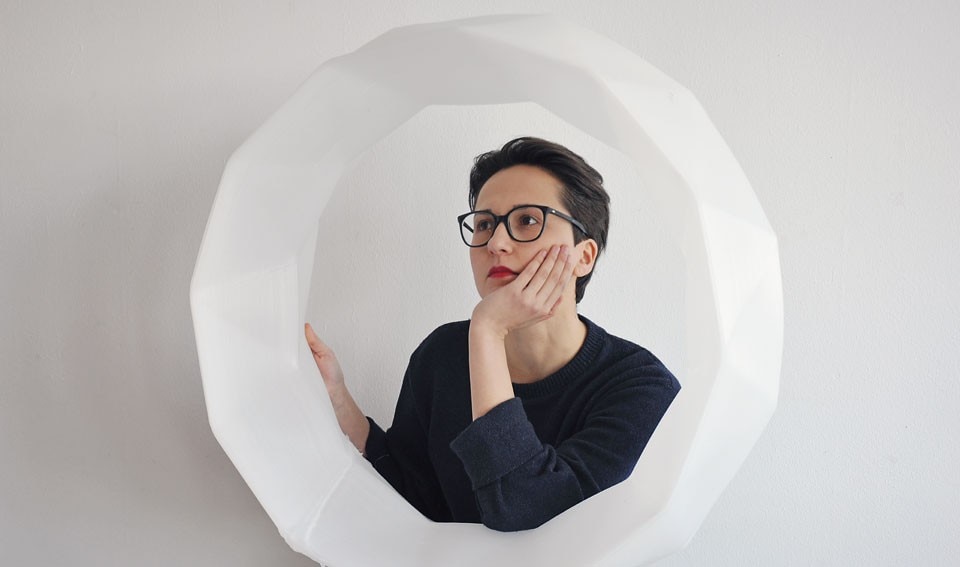

What if the edge could connect?
FLAT is the flush window born from a deep dedication to design; it speaks the language of architects, integrating seamlessly into diverse contexts.