Stefan Diez: On the one hand, the idea of working for a company that is so hugely important in the history of design is amazing. On the other, I chose not to use the technology that made Thonet famous all over the world because it requires two people to do it and is very expensive. Making a good product for Thonet, now, means you have to respect history and contemporary constrictions, restrictions and circumstances. I find this quite interesting; it changes your perspective. I am drawn to developing the design with the manufacturer rather than taking a finished design and finding someone to produce it. I think it is far more difficult to work for a company that doesn’t know what it wants or has no history and leaves you free to do whatever you like. I think that is extremely difficult. In this case, I was trying to understand the history and find another distinctive dot along the red line.
GG: Do you think that boundaries and limits help creativity?
SD: I think boundaries are crucial in everyone’s work, not only mine. The moment there is a boundary, an obstacle or some kind of constraint, a designer can decide to find a way that is straightforward but takes a lot of energy, using traditional quality. But he/she can also choose to take a shortcut to the same goal. Like a clever driver who knows the shortcut, the best way, you use a technique to make something for the company or client. You do not know exactly where it will go; it is like a vacuum and not everything is pre-established. I see my job as defining this kind of free space in which to produce a design together with the company.
GG: You chose to work with wood. Was this material easy to deal with?
SD: Wood has a great quality, which is that it can be elastic without breaking. You can only do something like the 404 with wood. Sometimes, material and technique can back up the project. My approach is not to actually have something very specific in mind; it is more important for me to have a feeling or a kind of expression and I experiment to explore what is possible with the material; what the natural shape is and what emerges naturally. The results are surprising. A thing is never finished in my mind when I start work. As a designer, it is sometimes not good to work with the original material; it is better to look for a material that respects it and works just the same but is easier, cheaper and faster to work with. I use prototypes. Normally, I just try to find a substitute and, step by step, get closer to the material I want to use.
GG: Can we get closer to the 404 you designed for Thonet and presented in Milan last April. How the idea did come about?
SD: I met Peter Thonet in Milan and he asked me if I could conjure up a chair for them. I said “Of course, I can try!” One thing that was clear from the very first was that this design could not be simply a new chair, just a new shape. It had to be something that included a production process because Thonet was always famous for including a production process in its work. With its bentwood furniture and then its tubular steel furniture, Thonet has always been a company that mastered technology. It was also important to develop a small idea that could be used for an entire program, the 404. It is significant, manufactured differently from the company’s other products. What distinguishes the 404 is that legs and backrest, everything, is curved in one dimension but all the elements come together in this sort of node, which is formed three dimensionally. It is quite new technology and you can increase the thickness in the centre. All in all, the way the chair is made is unique. I don’t think it is like any other chair. It is not technology, e.g. that of bentwood, that makes the chair special but the way the parts come together.
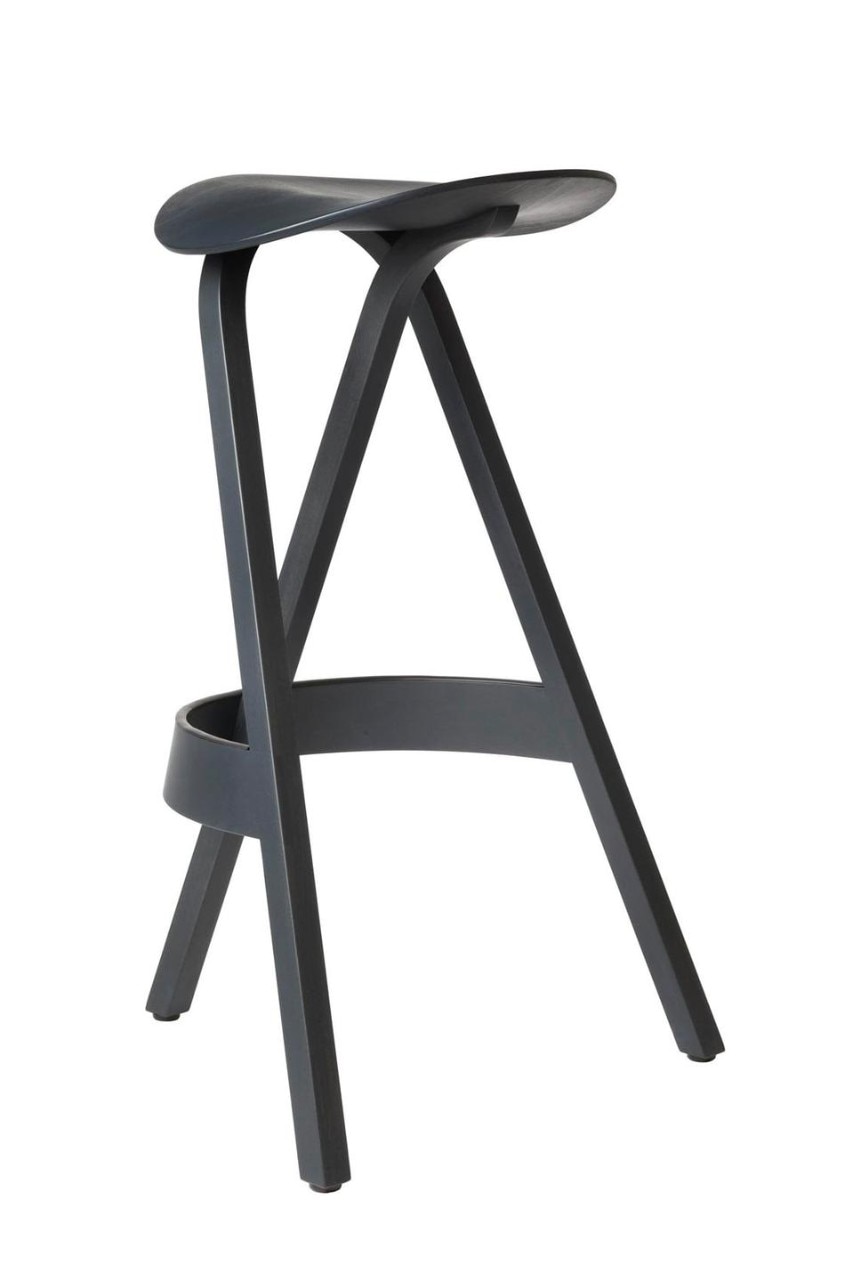
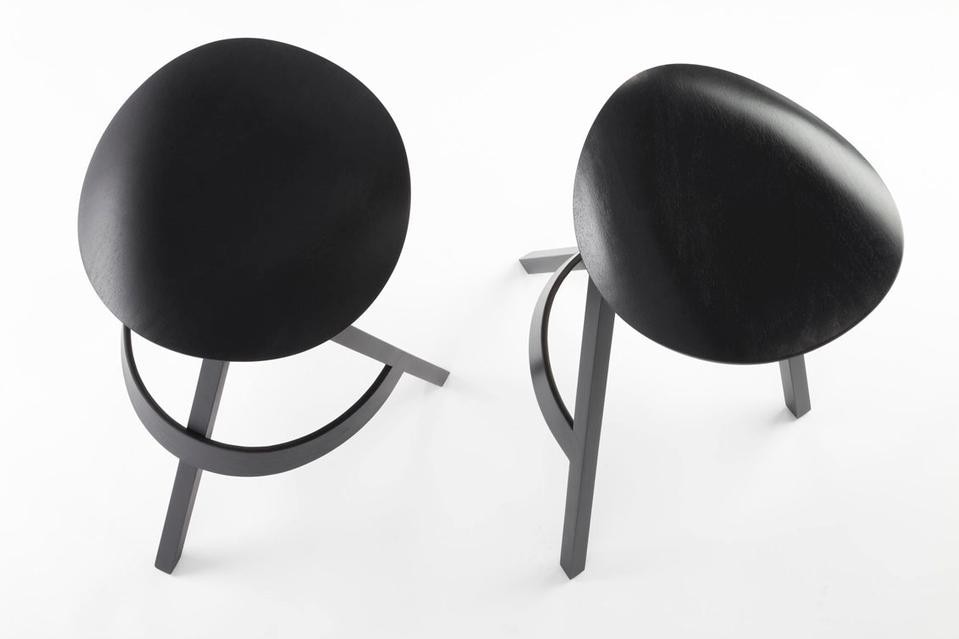
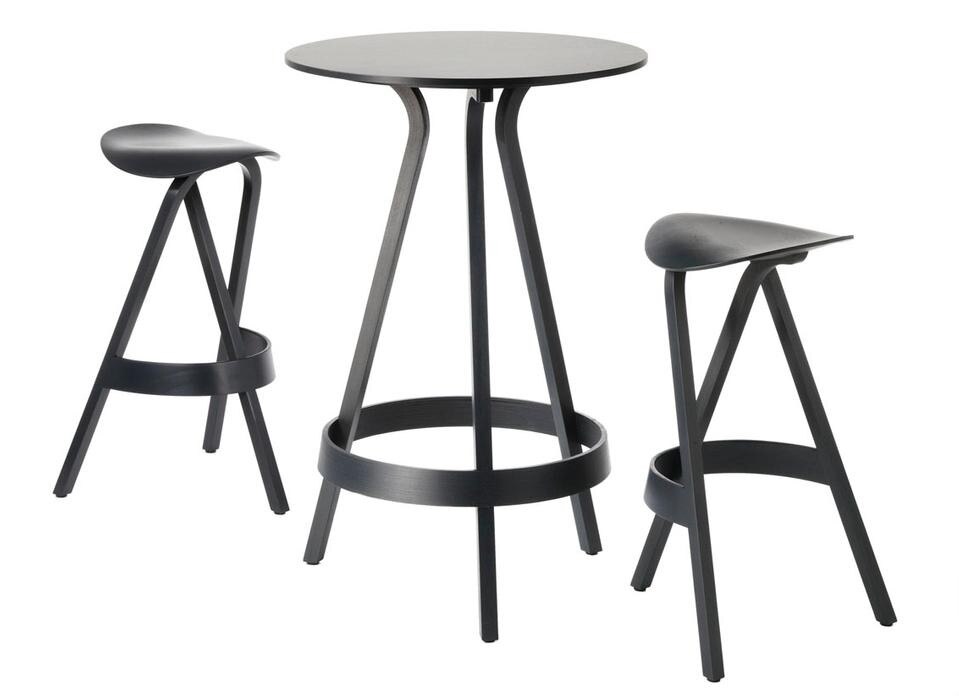
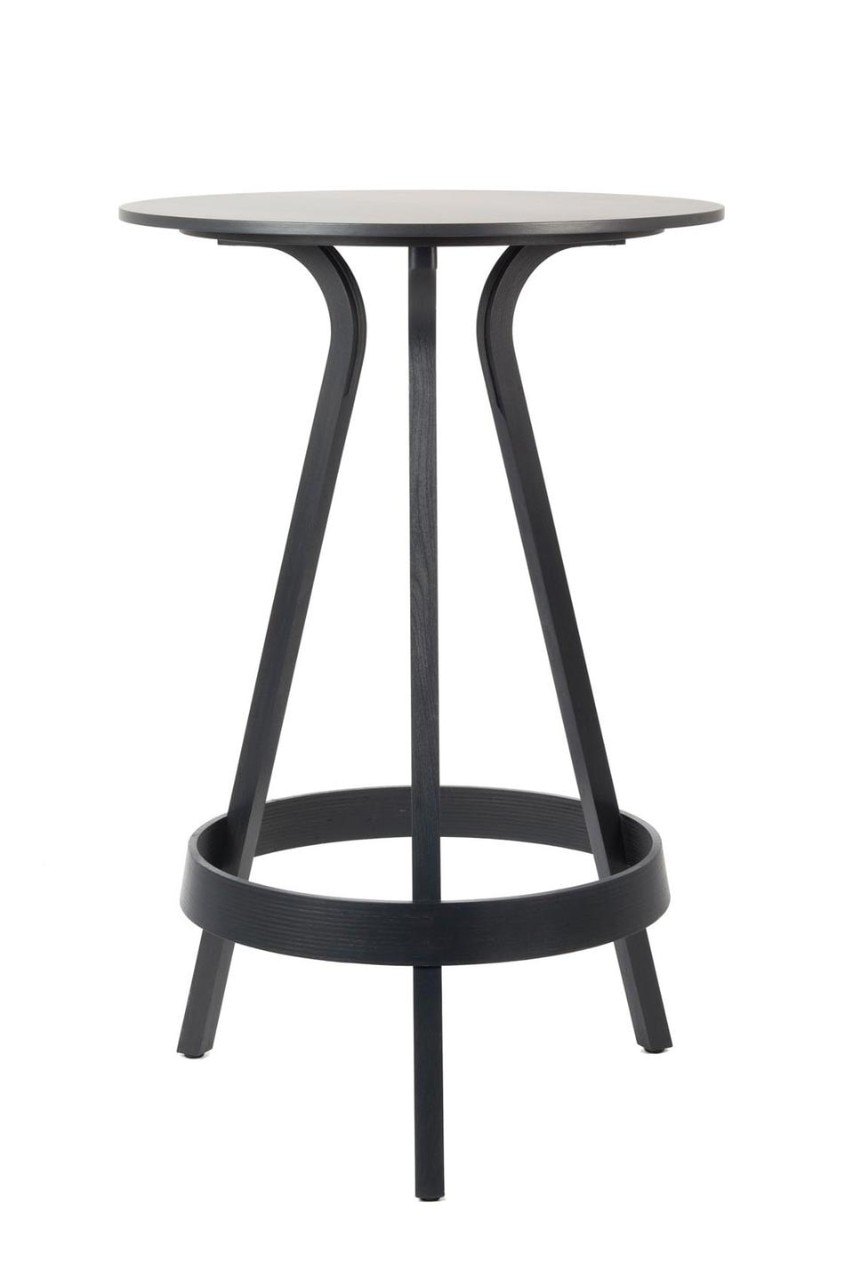
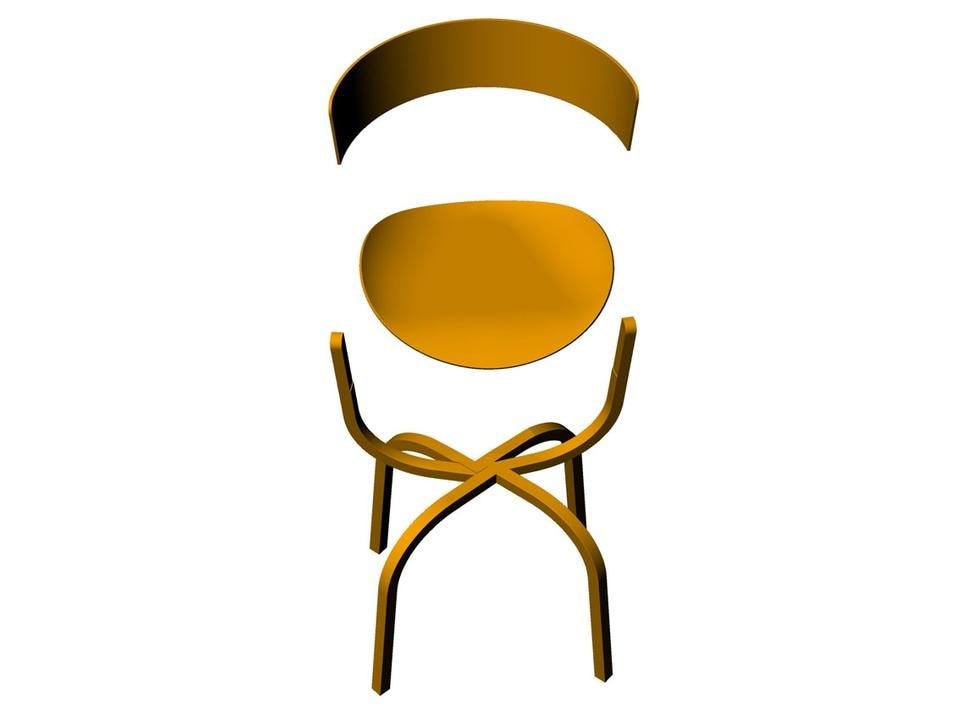
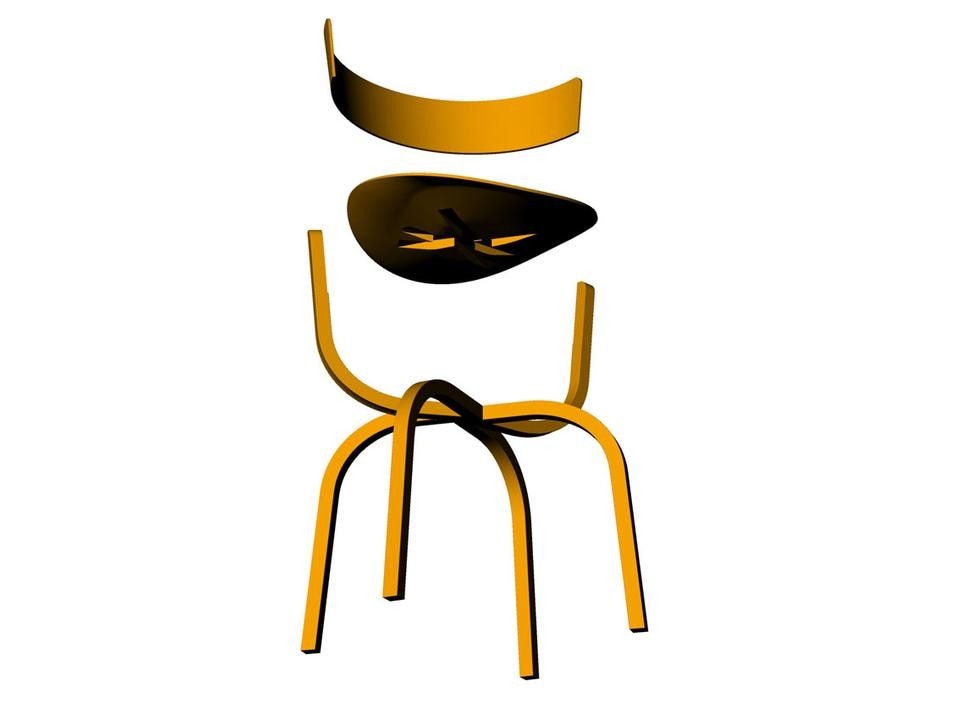
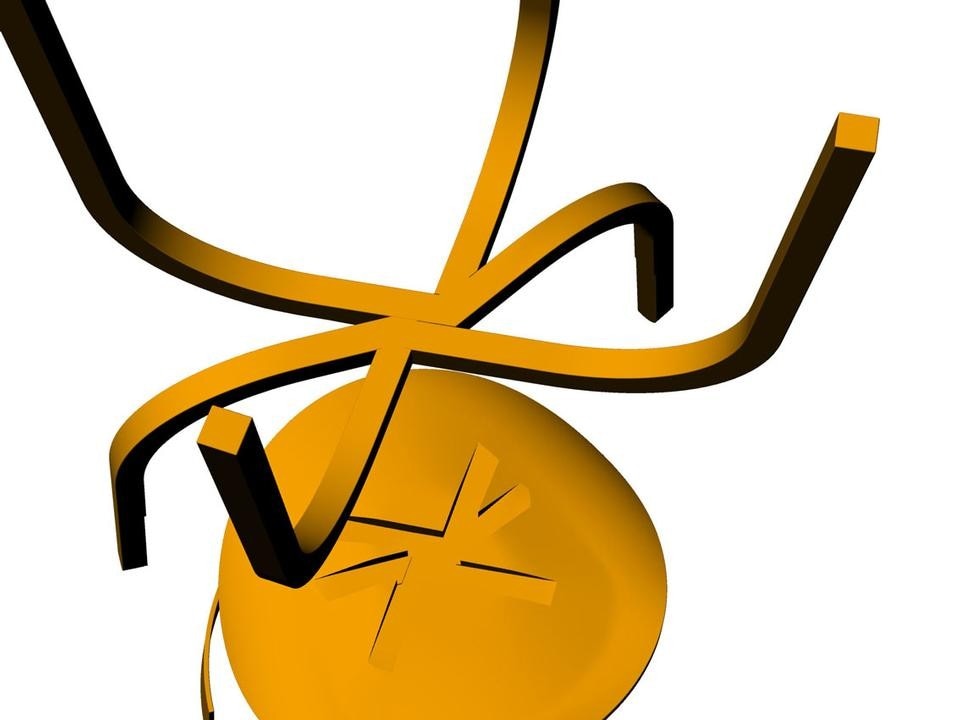
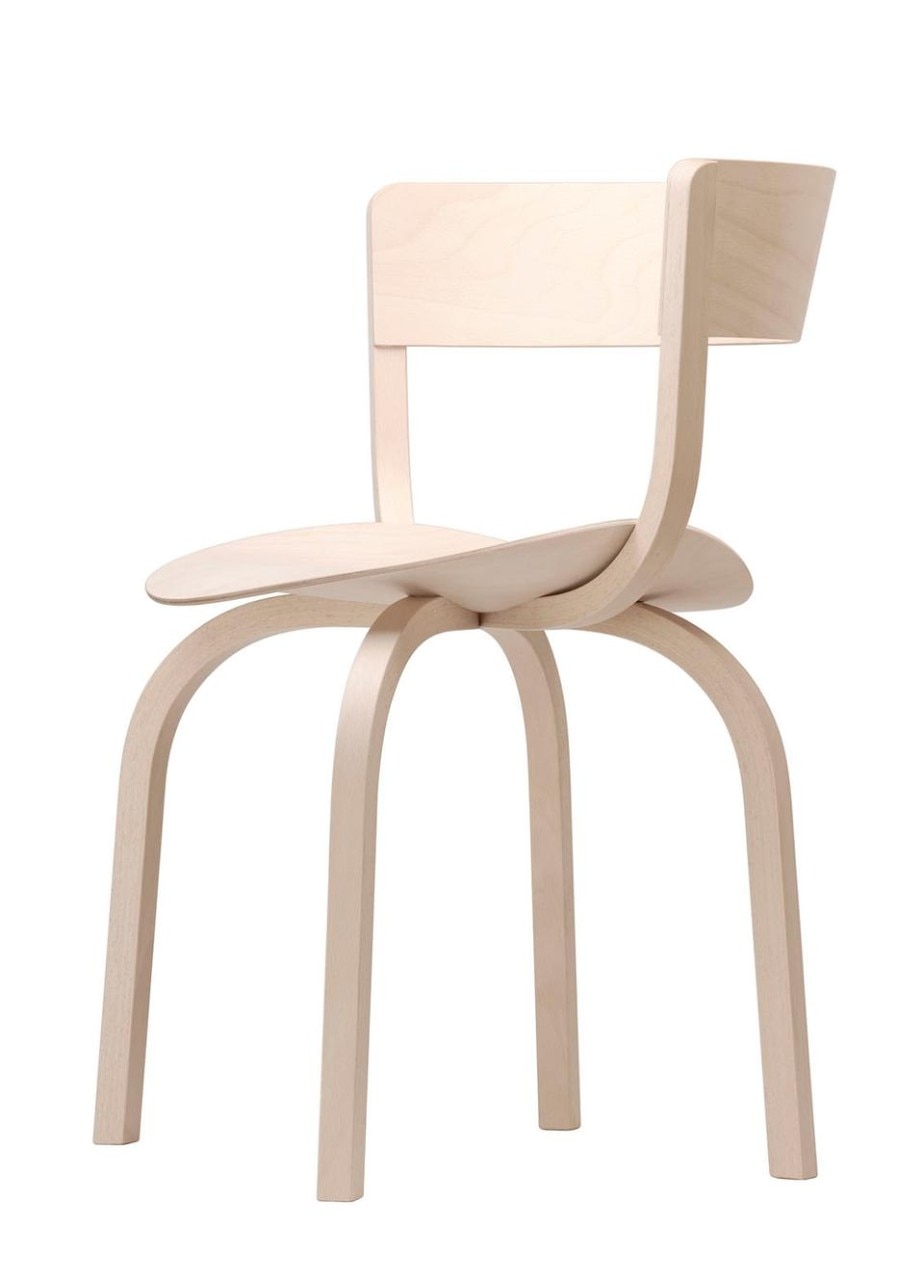
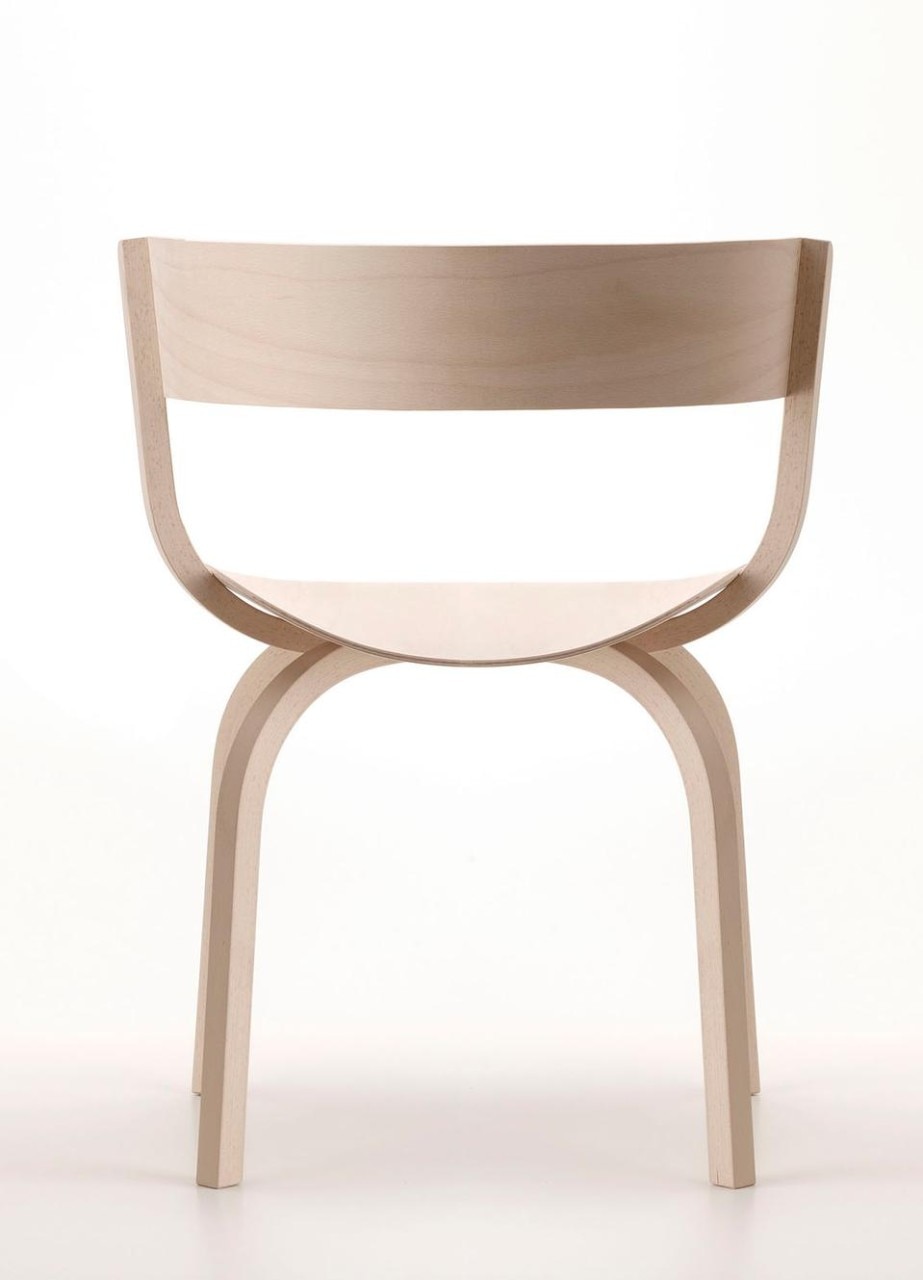
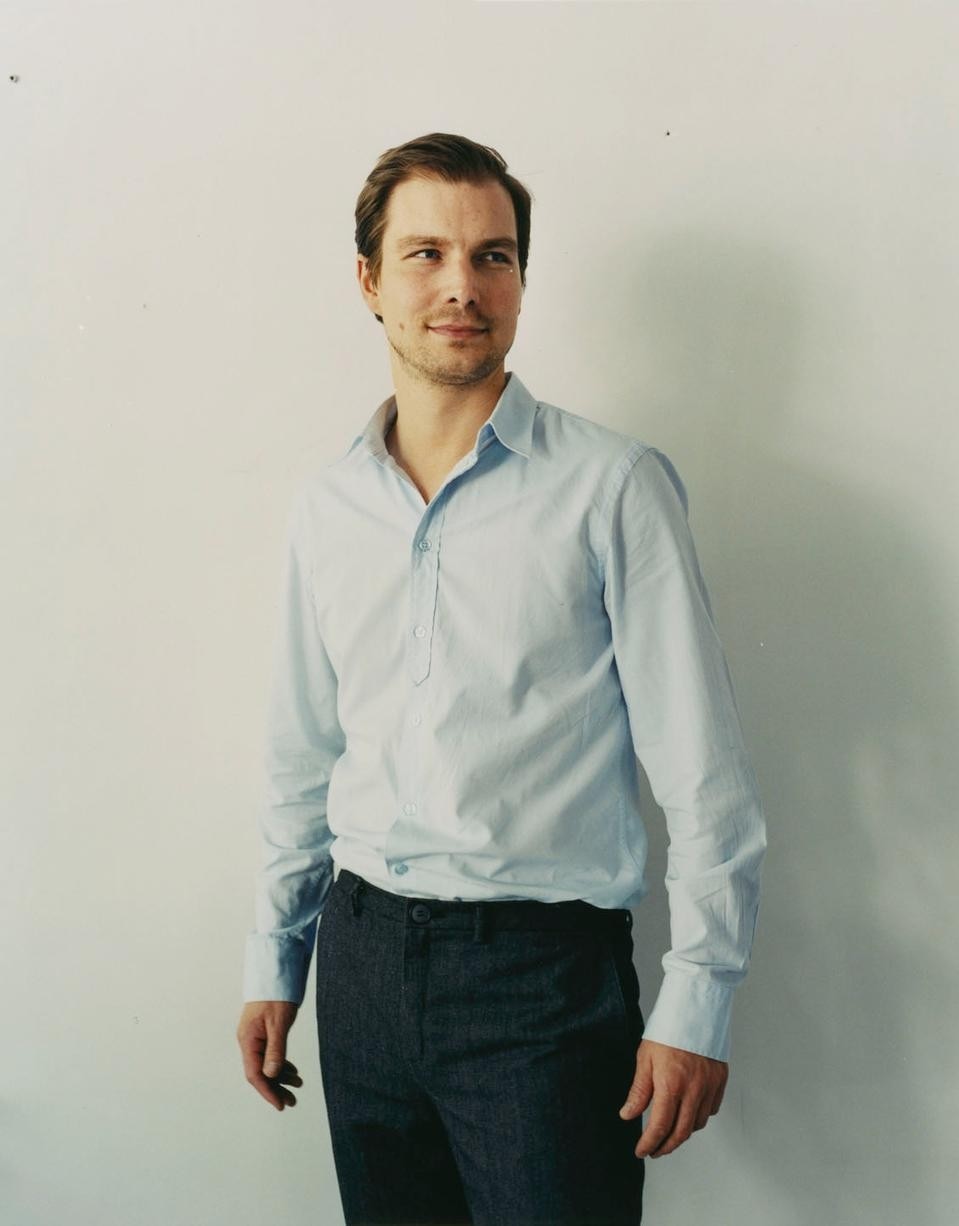

Tomorrow's energy comes from today's ideas
Enel extends the date to join the international “WinDesign” contest to August 30, 2025. A unique opportunity to imagine the new design of wind turbines.