Alberto Meda, Paolo Rizzatto
Mix light for Luceplan, Milano
Research from an Industrial Viewpoint. Our objective was to design a lamp with light-emitting diodes that would closely resemble an industrial project, seeing that one-of-a-kind pieces are not that interesting to us. We had gained experience with an experimental project called StarLed, which had a few limitations regarding its luminous efficiency, but which was useful because we built up relationships with a number of people. This helped us to involve manufacturers of components and convince them to participate in this project with us.
The Functioning of LEDs. All LED technology is based on semiconducting materials. A LED is a diode with a sandwich construction. One of the layers has positive charges in excess; the other is doped to increase the number of negative charges. When you make electricity flow through the diode, the two layers of electrons get excited: the first layer gives off the electrons it has in excess and the second one grabs them. This recombining act sees the happy layers emit a photon. This is just a slightly poetic interpretation of mine, but approximately, it works like this: semiconducting materials emit light when electricity passes through them. There are currently many interesting experiments being done with semiconducting polymers, but we limited ourselves to using the more traditional LEDs with semiconductors such as silicon, gallium, arsenic, etc.
The Urban Planning of the Circuit. Behind the design of this lamp is the desire to establish a different kind of relationship with the world of electronics. In general, electronics is seen as a separate world – impenetrable and so incomprehensible that it requires an act of faith from its users: you give up trying to discover the logic behind it and accept that the only thing controllable about it is the interface. We, however, wanted to get involved and find out things. We were interested in understanding if it were possible to change the process and produce a formal result by starting out with purely functional questions. Entering the logic of LEDs implies the concept of miniaturisation. The essential trick is to change your viewpoint. If you approach it from close up, you’re able to enter inside and start trying to figure out the logic that rules this microscopic world. One of the tasks we took on with this project was to use the possibilities of electronic circuits without blindly adapting to the logic that governs them. Rather, we sought to control them, even in their formal aspect, in order to come to a new design. In an electronic circuit it is possible to think about changing the distribution of its components in an urban-planning kind of way. It’s a question of scale. If you study the design of electronic circuits from up close, you can understand how the pattern of the circuits corresponds to real and precise functions. Some are very beautiful. You can distinguish paths and tracks that are not allowed to touch, like in a labyrinth. In the end, the logic is almost banal. They are just very tiny worlds. When we came to zoning the printed circuit, we tried to position the most voluminous blocks in a certain place. We put the condensers and the memory files (as if they were skyscrapers) towards the back, leaving more space for the logical devices (like single-family homes) and saving a little room for some greenery. The goal was to get the minimum surface needed. In the end, we had a circuit that looked like a kind of garden city.
Power and Cooling. In order to survive, LEDs can’t heat up beyond a certain temperature. It is not true that LEDs are cold. They heat up like everything else that has power. Before, when they had no power and didn’t give off any light, LEDs were thought of as not producing heat. Our lamp uses six Watts, and six Watts produce heat. The technology we used is called “Chip on Board” because there is a chip that electronically unites the LEDs. The inside of it contains (on a microscopic level) all the necessary connections. The “on Board” means that the circuit is mounted directly onto a plate, and in our case the plate is made of aluminium. The design of the circuit and its relative mounting on this kind of “board” is a process that was done especially for us. Our trick was putting everything on an aluminium plate in order to dissipate heat. This means that the very plate the LEDs are attached to was studied to function as a radiator. We wanted to follow simplification logic regarding the cooling problem, too. In fact, ours uses convection cooling which is very simple. Naturally, seeing that the plate is pretty thin, the dispersion surface needed to be as large as possible. This is where the design of the head comes from, and its dimensions are directly related to the LEDs’ cooling needs.
Shape as a Result of Different. Necessities The head is a sandwich made of two sheets of metal with the circuit in the middle. The shape (urban layout) of the circuit was only possible thanks to close collaboration with the electronic circuit builder, because obviously he did not expect to have to follow the design with a specific aim. We can say that in plan, the city could have been different, but we forced it to follow our design. We showed it the way to go: down this road, then turn left. The problem was organising all the electronic parts: the lenses, the condensers, leaving room for the switch, keeping free space for the movement of the filters that swivel on a pin and allow the temperature of the light to be changed. In fact, the standard circuit is a round stamp, and we asked ourselves: what if we move this component over here? We started an exchange, and the name Mix comes from the mixing of different expertises. As for the shape of the lamp, we wanted to emphasise extreme flatness, because the advantage of LEDs over all other light sources is that LEDs are a flat surface. LEDs have a thickness comparable to a few tenths of a millimetre. So the size problem has more to do with the apparatus needed to make it function better. The great thing about using LEDs is trying to express things that another lamp could not. Using a small subterfuge, we tried to make the head thinner by grouping all the larger components in the centre so that the perception of its flatness would not be altered and remain as slender as possible. From a conversation with Alberto Meda and Paolo Rizzatto
Vico Magistretti
Lampada Tikal for FontanaArte, Milano
Constructing a mobile piece of geometry that will regulate light flow is the concept behind the Tikal lamp presented at this year’s Milano Furniture Fair by Vico Magistretti. It is an evolved form of an old patent for a lamp with a variable light flow that he registered in 1972. Before that patent, other lamps applied the same concept, in particular the Dalù and Eclisse lamps which Magistretti designed in 1965. He said: “The shape has changed because the bulb is different. Take Eclisse: it burnt for two or three generations. Today, with fluorescent lighting, it doesn’t burn anymore.” Although Magistretti starts from the assumption that “it is not a sophisticated object, technologically speaking”, the sophistication lay in how the design deviates from the standard geometry constructed around two hemispheres that revolve on the same axis and form the basis for the idea of the movement. Magistretti achieved the misalignment and asymmetry of the helmet form via gradual adjustments, working directly on the body of the lamp. It is made up of mobile parts but does not display any mechanical elements that suggest the origin of the movement. The overall form is a jointed mobile body that changes according to the reciprocal positions in space. We asked Magistretti whether the design seen at the time of the first patent alluded to the kinetic art research in vogue at the time. He replied: “I never think about these things. It is simply an adjustable bedside lamp that can be closed slightly in order to adjust the light flow.” F.P.
Ross Lovegrove
System X for Yamagiwa, Tokyo
The luminous pattern that Ross Lovegrove adapted to the scale of architecture displays a type of sophistication that is rooted to the project’s relationship with industrial manufacturing. In its finishing, details and use of materials, it shows the kind of perfection that can only be the fruit of an industrial approach, where each part is resolved in minute detail thanks to a painstaking process of experimentation and verification (and this can be read in Toshiyuki Miura’s technical report). It is enough to look at the design of the slightly curved fluorescent tube (specially made by Yamagiwa’s lighting engineers, and currently awaiting a patent) and see the modules come together without compromising the uniformity of the emitted light. It is the sophistication of this rapport that Lovegrove puts on display in creating this system that could be placed in the category of “architectural devices”. In doing so, he opens an exchange between industry and architecture where design is used entirely to emphasise the enjoyment of experimentation with industrial manufacturing, (“They have access to technology that we don’t have; plus, they take pride in solutions that are well-made”, Lovegrove says). Hypothetically, the X module can be repeated endlessly and has endless combinations. The joined modules diffuse a light that emanates all along the surface like a luminescent skin with the ability to regulate its intensity and colour. Contributing to the creation of uniform luminescence was the precise control of the intensity of the reflection and the shadow area over the surface caused by the inevitable opacity of the material and the attached parts. This problem was studied in depth by technicians who were charged with taking volume away from the lighting system. Connecting the X modules follows a cellular principle to create light structures that can be regulated: areas with different colour temperatures can be made that are controlled by a computerised system, which in turn can be controlled by an electric switch. The lighting element, its connecting parts, the materials and the metal hardware were all selected for their capacity to diffuse, reflect or contrast light. The technicians and engineers experimented with the material not only in regards to its weightlessness, but to counter its opacity (an impediment to the diffusion of light). As a result, they obtained the uniformity that makes the illumination appear as a release of some mysterious energy contained inside the material. F.P.
Richard Sapper with Nicole Sargenti
Halley lamp for Lucesco Lighting Inc, Palo Alto, CA
In the autumn of 2003, an upstart Silicon Valley company that wanted to develop LED technology for lighting applications asked me to design a lamp. I have no idea why they asked me but one reason may be that I designed Tizio thirty years ago. I never designed another work lamp after that piece. So I was initially very sceptical when they asked me because the white LEDs I had seen up to then produced an irritating light, while I consider the colour of light to be of fundamental importance. I can’t stand fluorescent lights; they make me feel as if I am enveloped in fog because the light source is diffused and not focused. This type of light source lacks the sense of “a little sun” that traditional bulbs have. This was not a problem in the case of LEDs but the colour problem remained, which I found unavoidable. When the Lucesco technicians promised me they could alter the colour of the light with their technology – and, indeed, we managed to produce the most natural light possible – I was willing to embark on the design of a new lamp. Although I imposed no restrictions on myself, I thought it would be interesting to go back and examine the issue of the work lamp that I had addressed thirty years earlier. Thinking about this again and the way I had approached the design of Tizio, I remembered that the project had been created in response to a personal need of my own. I can say that Tizio was designed to produce a work lamp that was right for me. I realised that my needs had not changed greatly since then. I had to construct a lamp that would allow me to move the light source as easily as possible, bringing it closer to my work desk, the book I was reading or the sheet of paper I was drawing on. That is why I needed a very small reflector, because a large one gets in the way if it is too close. I also needed the base of the lamp to be as far as possible from its top, because my worktable is always a mess and there is no room near me for the base of a lamp. Therefore the lamp had to have very long arms and a balanced and quick movement, not held back by springs and friction but totally free. wanted the top of the lamp to move gracefully in all possible directions. All these had been requirements for Tizio and I knew the needs had not changed much since then. What has changed over the last 30 years is the technology. It seemed right to try and design a work lamp that applied all the technology that had become available since then. I started with the light source. Advantages of LEDs LEDs present major advantages compared with halogen lights. First and foremost, they only use a quarter of the electricity and, if properly cooled, they will last 20 years when used regularly for eight hours a day. Another benefit is that they are very small, so I could design an even smaller head than the one for Tizio. Moreover, I wanted to create a lamp that was far more mobile than Tizio. I wanted to have six three degrees of freedom instead of just three, yet still have a counterbalanced movement - completely free and with just the minimum friction to guarantee the stability of the positions adopted. So I designed six freely revolving joints that move through 360 degrees. There are no wires, the electrical connectors are hidden inside and I used hinges from laptop computers, something which I have been designing for the past 25 years. LED cooling power The real problem of high-power LEDs is the way they heat up. Although the heat produced is far less than that of a normal bulb, LEDs do get hot. The difference is that although a normal bulb will work normally at high temperatures, heat quickly destroys LEDs. All the lamps seen on the market today use low-power LEDs that offer little illumination, because it is hard to cool high-power LEDs. The problem is similar to that of cooling computer CPUs: a "heatsink" is normally used and consists of a large aluminium fin assembly. This solution was not available to me since the top of the lamp would become too bulky and heavy for my purposes. In order to create a system of multiple counterbalanced arms, the top of the lamp must be light enough to avoid having to multiply the weights needed for the gradual balancing of the system. How could I resolve this contradiction? Notebook computer technology came to my aid once again since laptops have CPUs that need cooling. Every gram of weight is precious and every millimetre fought over. As a result, Halley now has a very sophisticated cooling system: the LEDs are mounted on a thin aluminium plate joined to a so-called "heat pipe", a slender copper pipe containing a cooling liquid that carries the heat to the radiator. The radiator is also very small but operates like the one found in a car, with a fan that moves the air through the cooling flaps. One interesting detail is that the liquid passes and returns through the same pipe without mixing; it goes along the sides and returns through the middle. Astronomical analogy The design of the top of the lamp slightly resembles a comet in my view because it has a luminous top and a tail. That is why I called it Halley, in memory of the astronomer who became famous for the comet that bears his name. This reference to a comet is not limited to the shape of the top but also refers to its movement and the way in which it was conceived. Compared with Tizio, which has a symmetrical structure, two pairs of arms and moves a little like a crane, this lamp has a set of asymmetrical arms. There is a fundamental asymmetry in its construction which permits free movement. In order to achieve perfect balance, I needed a lateral counterweight that would compensate the weight of the final arm. This counterweight is a chrome ball that represents the Earth around which Halley circles like a small comet in my imaginary astronomical picture. From a conversation with Richard Sapper
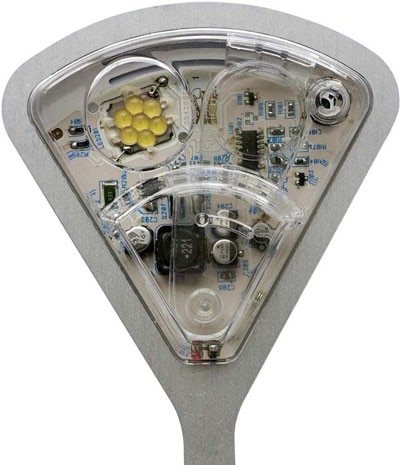
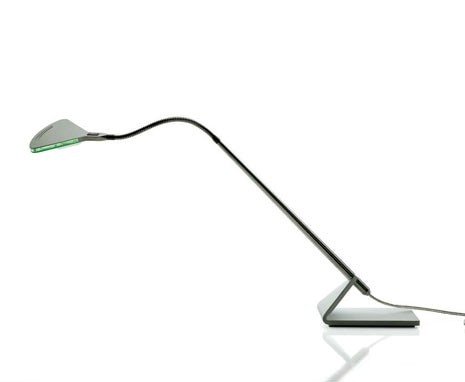
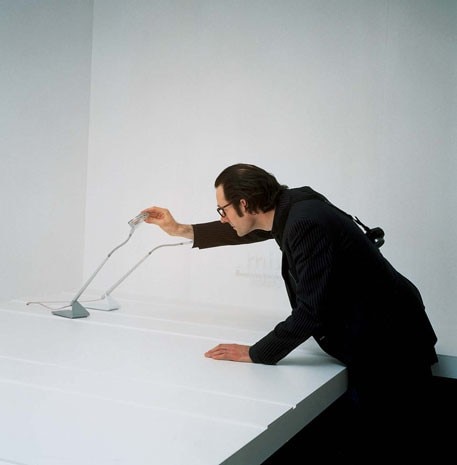
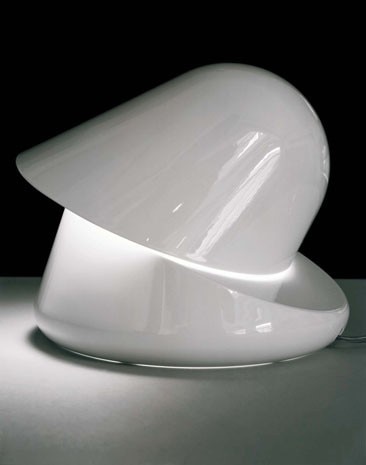
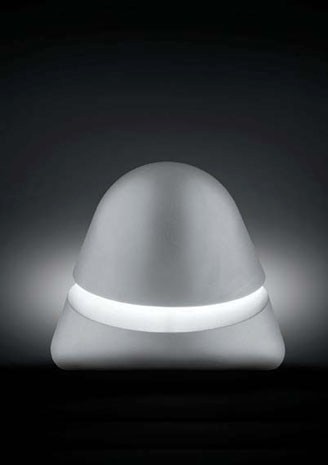
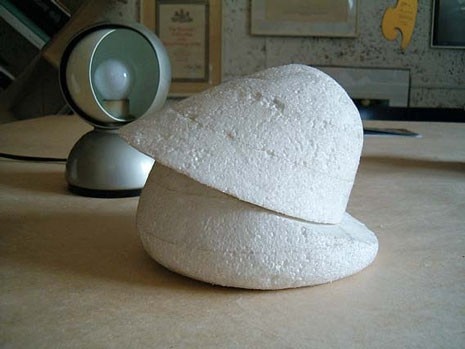
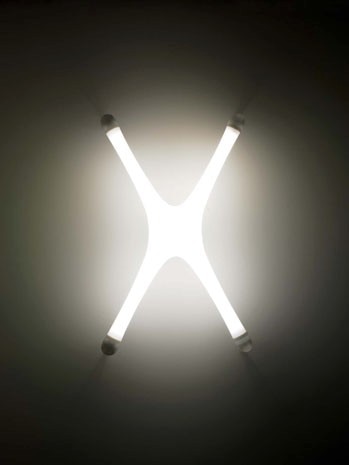


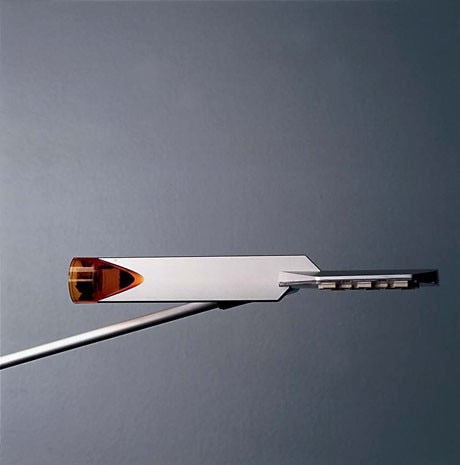
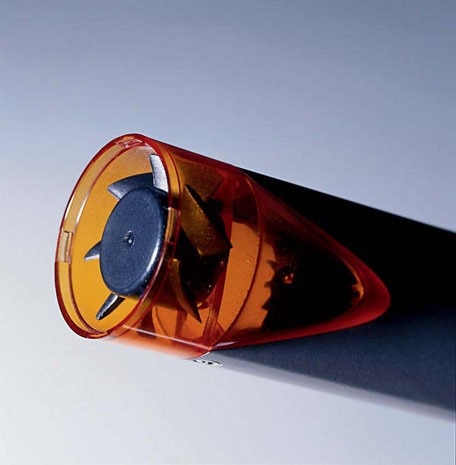

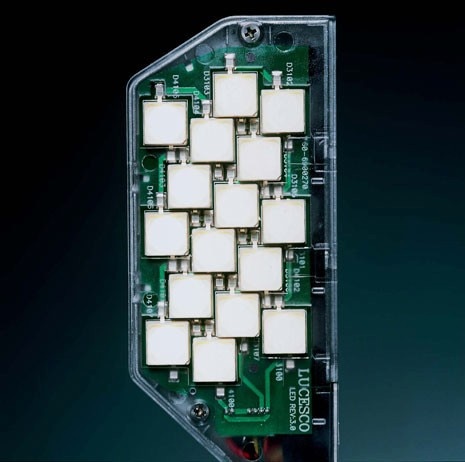