The latest news is that Dyson has developed a new ventilator after having received an order from the British Government for the production of 15,000 items. In the meantime, Gtech, another UK appliance manufacturer, is working on a prototype for assisted respiration in response to the same request from the government. In the United States, Ford has joined other car manufacturers, such as Tesla and General Motors, who have converted their production lines, lines that have almost ground to a halt due to the effect the pandemic is having on consumer demand. The Spanish government has announced that Navantia and Airbus are working on producing equipment for artificial ventilation. In Germany, where ventilators for intensive respiratory care were already abundant at the beginning of the epidemic, the German company Draegerwerk - which develops and produces technological equipment and systems for the medical sector - will be manufacturing 10,000 ventilators for the government, equal to a standard year’s production.
In the meantime, in Italy, alongside efforts concentrated on reconversion, above all from fashion brands, the workshops of makers throughout the country are saving hundreds of lives by responding at an incredible pace - through 3D printing - to the growing demand for assisted ventilation equipment for patients affected by Covid.19 that cannot be satisfied by the global production and distribution system, crippled by the spreading of the virus. What has made this little miracle of self-production possible here in Italy? We asked Massimo Temporelli, founder of The Fab Lab Italia and one of the key figures in this process. According to Temporelli, “in Italy, more than in other countries, micro-enterprise is part of our DNA, and artisan knowledge is more present than elsewhere”. This stronger sartorial skill seems to be the element that characterises the response that the Italian production chain has managed to provide to the national lack of medical intensive care equipment during the Covid-19 emergency.
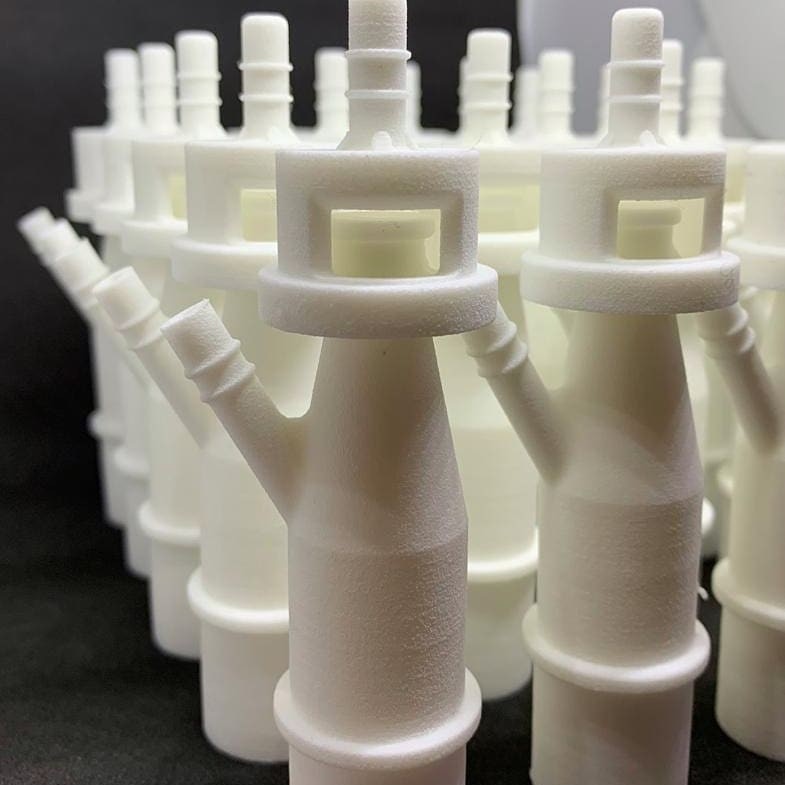
But let’s look at how this story played out. At the beginning of the spread of Covid-19 in Lombardy, Brescia was one of the worst-hit provinces. It is here that, on 13 March, the call was made for supplies of valves (Venturi tubes) for reanimation ventilators. At the hospital in Chiari, in the province of Brescia, the valves were running out, and the supplier was unable to get hold of more in the short time necessary. It was at this point that Nunzia Vallini, the director of the Giornale di Brescia newspaper, contacted Massimo Temporelli, who in turn - unable to easily move from Milan - called on a company in the Brescia area, which took the valve from the hospital to then redesign and produce it with a 3D printer in the space of just a few hours. This was the first item to be produced by Isinnova, a Brescia-based start-up that was generally unknown until then.
Elevated sartorial skill seems to be the element that characterises the response that the Italian production chain has managed to provide to the national lack of medical intensive care equipment during the Covid-19 emergency.
The owner of the original file for the Venturi valve is an American company that was unable to share the design due to company policy, and so the valve was reverse engineered by Cristian Fracassi, engineer and founder of Isinnova. The file was not shared as open source as it is a complex design that cannot be produced with standard 3D printers, but only with sophisticated and less-common machines, and so Isinnova and The Fab Lab produce the items via two companies from the semi-industrial production chain that are printing them free of charge – Lonati for the Brescia area and Idea Factory for Milan – while they simultaneously respond to requests in their own zones (Bergamo, Brescia and Milan).
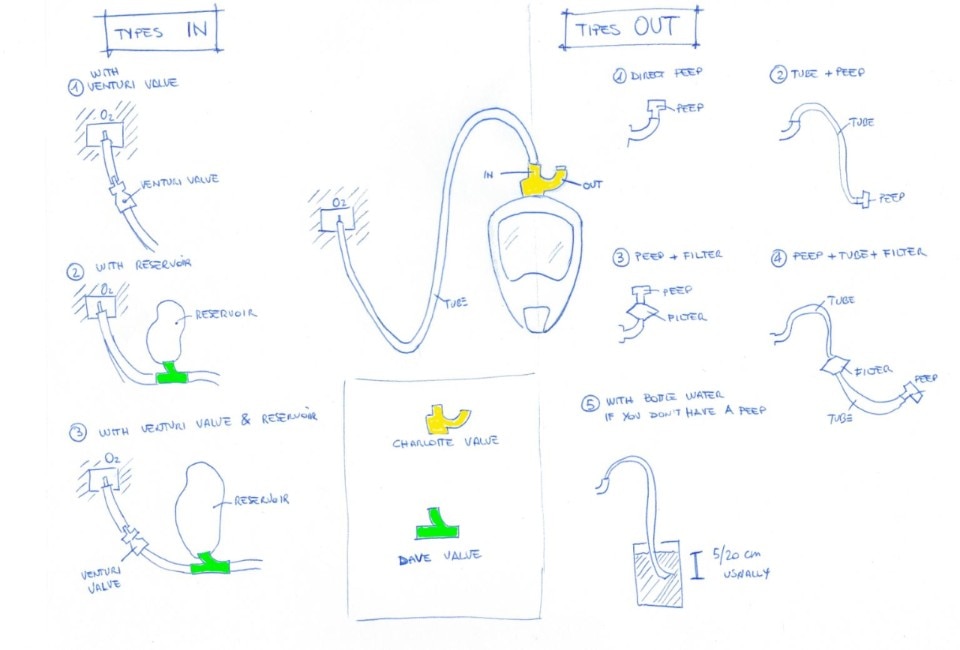
A few days after the success of the Venturi Meter, Cristian Fracassi was contacted by an ex-consultant from the Gardone Valtrompia Hospital, Renato Favero, who shared an idea in response to the possible shortage of C-PAP hospital masks for sub-intensive therapy, a serious problem connected to the spreading of Covid-19. The idea involved the construction of an emergency breathing mask through the adaptation of a freely available snorkelling mask. The rest is history: the French multinational that markets the Easybreath snorkelling mask was willing to collaborate with the request from the Lombardy region, providing the CAD drawings of the mask that was dismantled and studied, allowing the necessary modifications to be identified. The result was the designing of the new component for the ventilator connector, which Isinnova named the Charlotte valve, and which was quickly printed in 3D. The prototype was tested on a healthy volunteer at the Chiari Hospital, proving to be effective when connected to the ventilator unit.
The design of the Charlotte valve is relatively simple and can be printed with standard 3D machinery. All of the 3D-printing laboratories in the country are capable of printing it. “The response of makers to the Brescia emergency has been incredible” – reads the Isinnova website – “private printer owners and companies have offered to print the necessary parts. We have received the first batches, and over the next few days we will have the others necessary to make up 500 kits to be handed over to Civil Protection”. The call for the Brescia area is now closed.
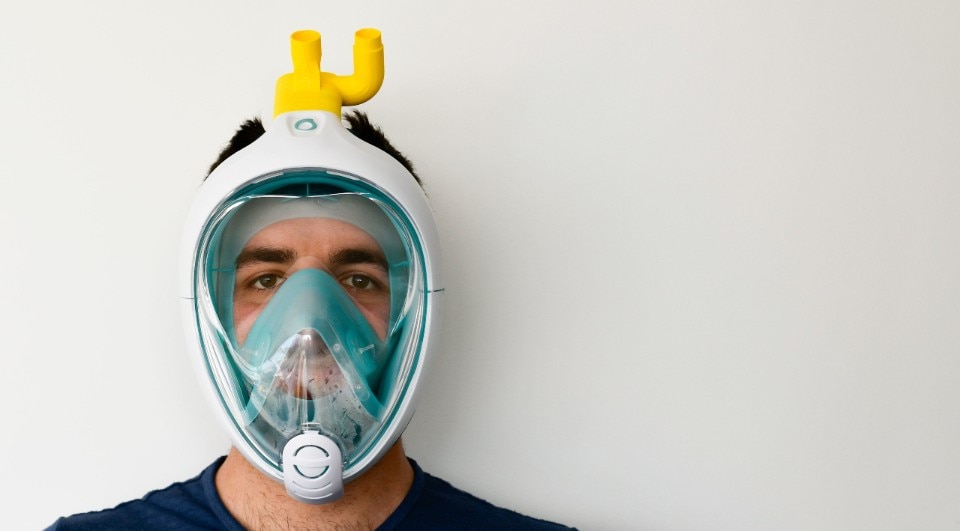
As well as a small initial supply, it has been announced that Decathlon Italia has just donated 10,000 masks to the Italian State, which will be distributed via the Regions and relative departments. “Now is the time for national coordination”, Massimo Temporelli told us, “we want Civil Protection to step in to coordinate the fantastic efforts of 3D-printing laboratories throughout the country with the various and pressing health requirements that are emerging locally throughout the regions of Italy”. In the absence of a direct channel of communication with the Regions, technicians, fab-labs and makers with digital production capabilities are called on to register on the website of the Make in Italy association in order to set up a national network. “We are asking you”, continues Temporelli in a Facebook post from last Friday, “to coordinate printing and assembly via the various local laboratories, creating a regional cluster. At the same time, it is fundamental to create a channel of communication with your Region to collect, modify and then distribute the masks.”
The scalability of this project risks being compromised by a “local-level” focus. “Where are the technological hubs? Manufacture has been delegated to the rest of the world. Would it not be wise to have functional centres in the various territories for the production of necessary items?” This is the question now posed by Temporelli as well as the other main players in this small Italian miracle. If there is anything to be learned from this story, it is that beyond good ideas and the ability to make them reality, what is also needed is increased centralisation and sharing of experience in order to capitalise on its worth.
- Project:
- Charlotte valve
- Typology:
- valve for ventilators
- Design:
- Isinnova
- Year:
- 2020

The New Brevo House by Pedrali
Brevo has given its Parisian headquarters, La Maison Brevo, a major makeover, prioritizing innovation and employee well-being for its 400 staff members. The furnishings, curated by Pedrali, transform the 3,000 sq m of interior and exterior space into dynamic, stimulating environments that foster collaboration and diverse work styles.