Konstantin Grcic: Even though we looked at some school furniture it didn't actually serve much as a reference. In fact, most school furniture seems rather out-dated and therefore offering little information for our project. From early on in the process it was clear that we were going to use a seat shell for making the chair. Therefore we studied all sorts of chairs using shells. There have been endless interpretations starting from the most famous—Arne Jacobsen's 3107 Model in plywood or Charles Eames' Fibreglass Chair, to the more recent Catifa chair by Lievore/Altherr/Molina for Arper. The seat shell represents a very common typology in chair design; it was difficult for us to find our own identity through both form and material.
What was the path that brought you to decide to use polypropylene instead of the "traditional" pagwood? What were the technical or functional reasons?
We were originally intending to use Pagholz as it is a technology closely associated with Flötotto school chairs. However, first test mouldings made us aware of certain limitations with this technology. Pagholz (like any plywood laminate) more or less dictated a two-dimensional geometry for the shell. Its production cost is relatively high and even in terms of environmental balance there weren't sufficient arguments supporting the Pagholz path.
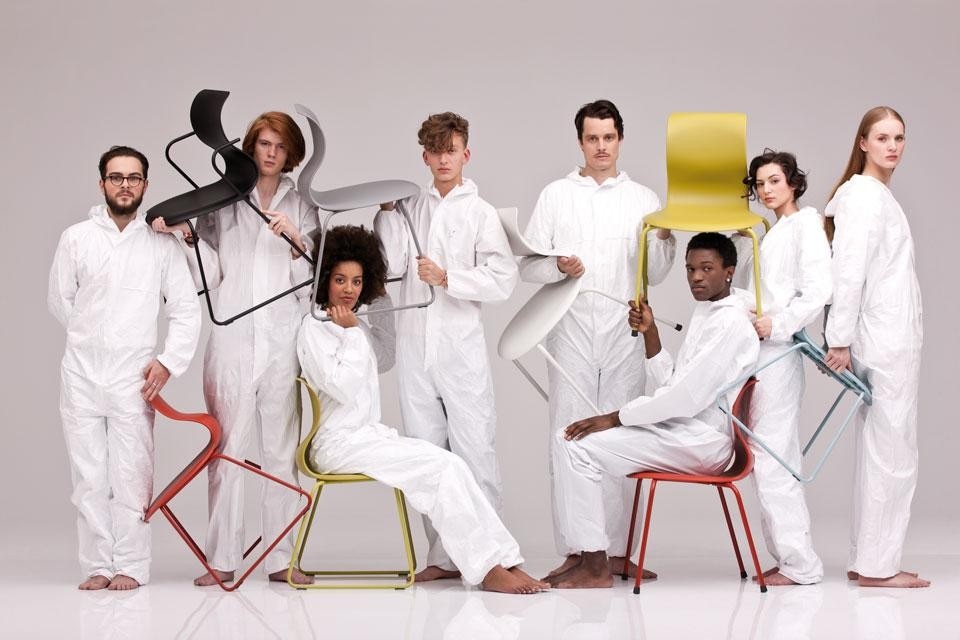
Above: an ad campaign shot by Oliviero Toscani for the new Pro chair by Flötotto.
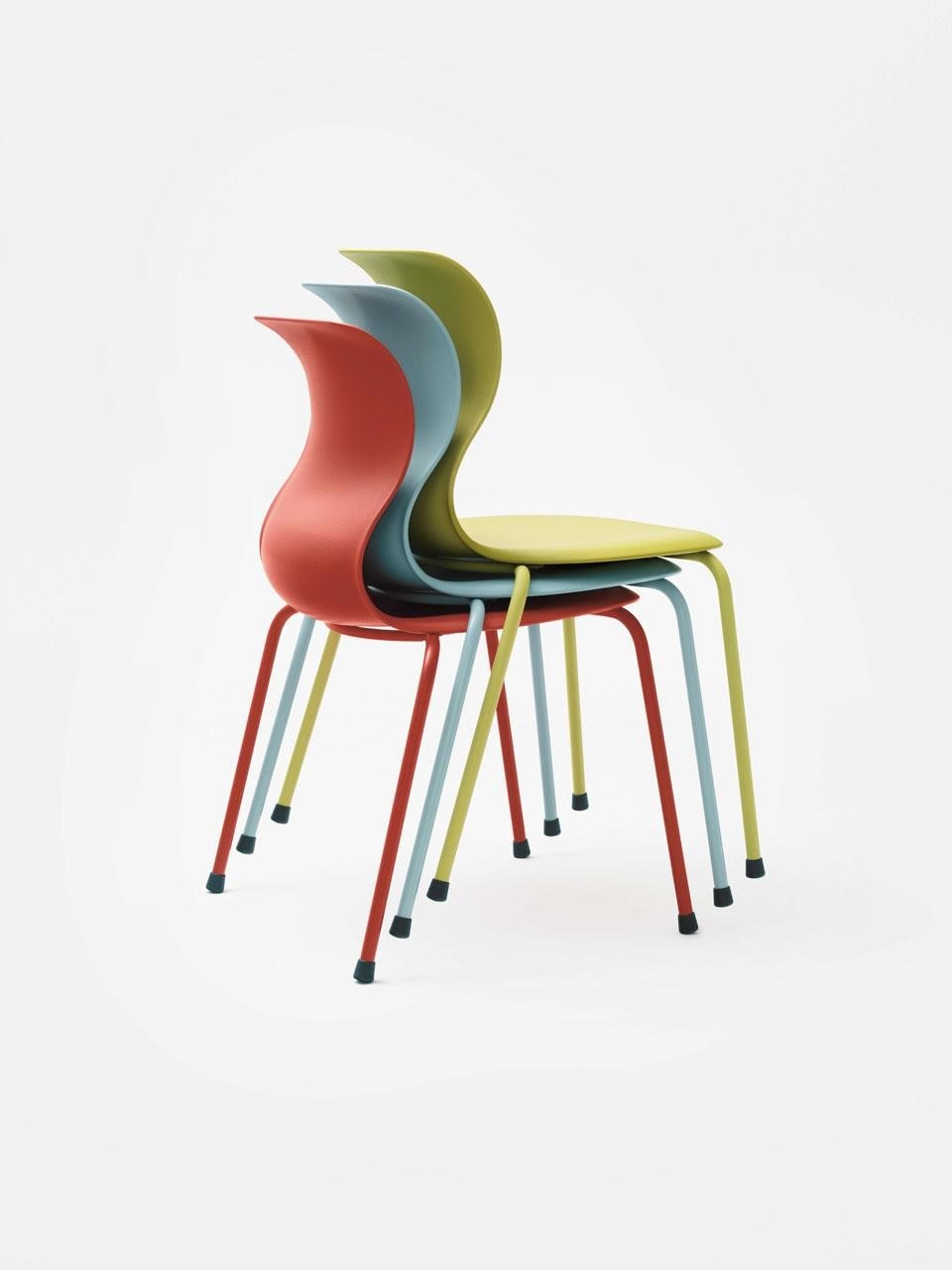
It has to be clearly said that wood doesn't necessarily equal environmentally responsible. The phenolic resin which is used to glue and seal the wood layers in Pagholz is anything but organic. Before switching from wood to plastics we were scrutinizing the pros and cons of directions. We made an effort to look into non-fossil plastics suitable for furniture production. A lot of companies now offer so called bio-plastics in their portfolios. However, these materials were not quite tested for long-term use in commercial projects such as ours. Either the performance/resistance of the plastic is insufficient or the price is too high.
Normally we can test the comfort of chairs ourselves. There is never a set formula for the right ergonomics of a chair, its an empirical process which means 'learning by doing'. In the case of the small chairs we were missing our own first-hand judgement.
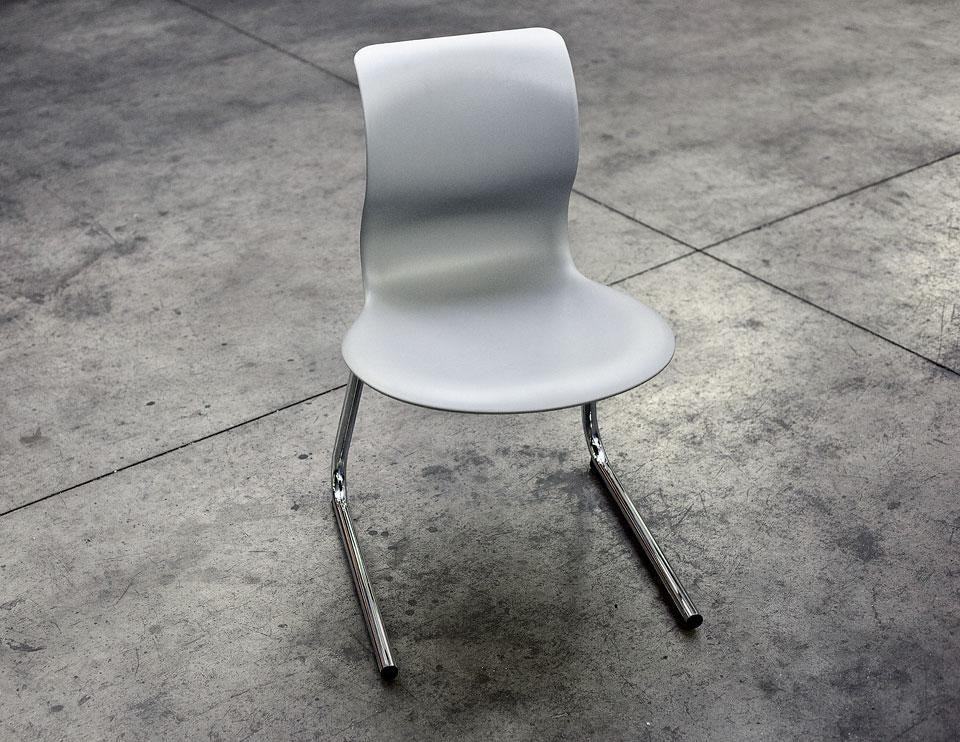
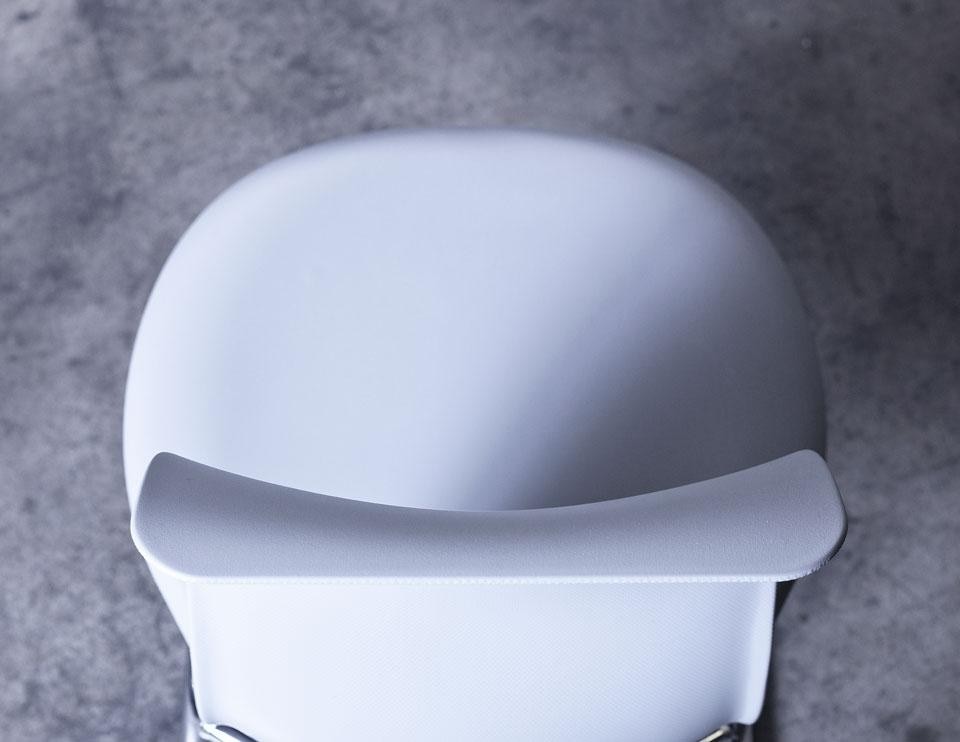
The biggest difficulty was designing the smaller size chairs, the ones for kids aged 6–14. Normally we can test the comfort of chairs ourselves. There is never a set formula for the right ergonomics of a chair, its an empirical process which means "learning by doing". In the case of the small chairs we were missing our own first-hand judgement. We could easily scale the geometry of an accepted adult size chair smaller, but who would give us an honest opinion about its comfort? Not that we didn't trust what kids say. However the analyses of comfort go far beyond an intuitive liking/disliking. As designers we have developed highly sensitized abilities for testing the comfort/ergonomics of a chair. For the project we ended up using a mix of methods: down-scaling, listening to kids' as well as our own objective judgements...and keeping our fingers crossed that we got it right.
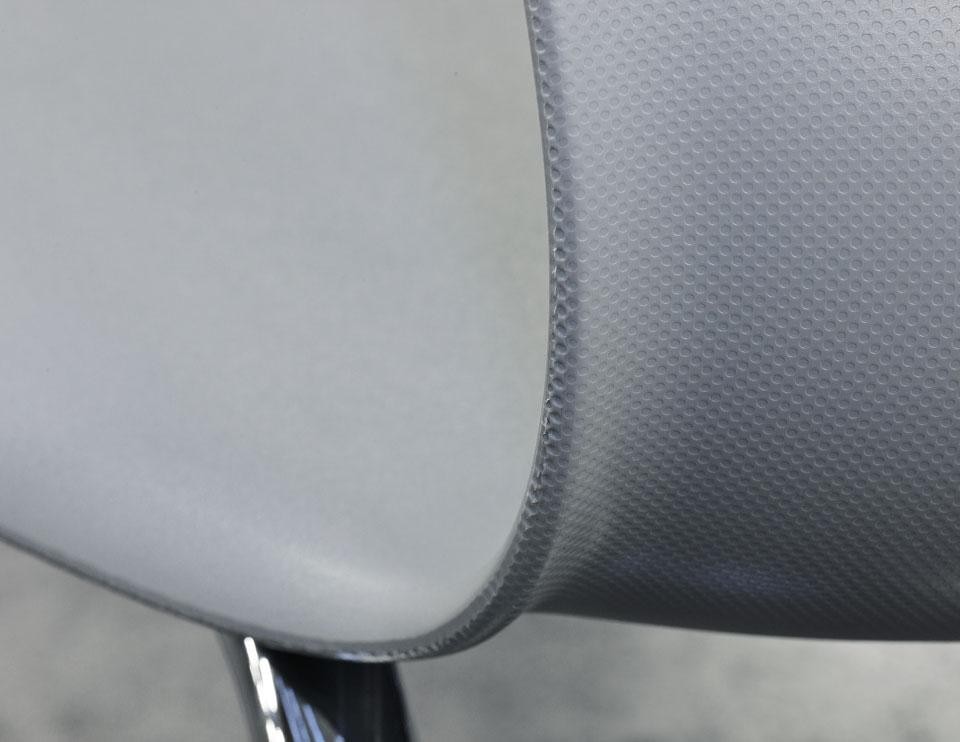
At the beginning we were trying to talk to (nearly) everyone related to our project: the kids of course, the teachers, the school's janitor, the people in charge of specifying/buying school furniture, the producers, even insurance companies. We wanted to find out as much as possible about the different criteria of a school chair as well as understanding the mechanics of its industry/market.
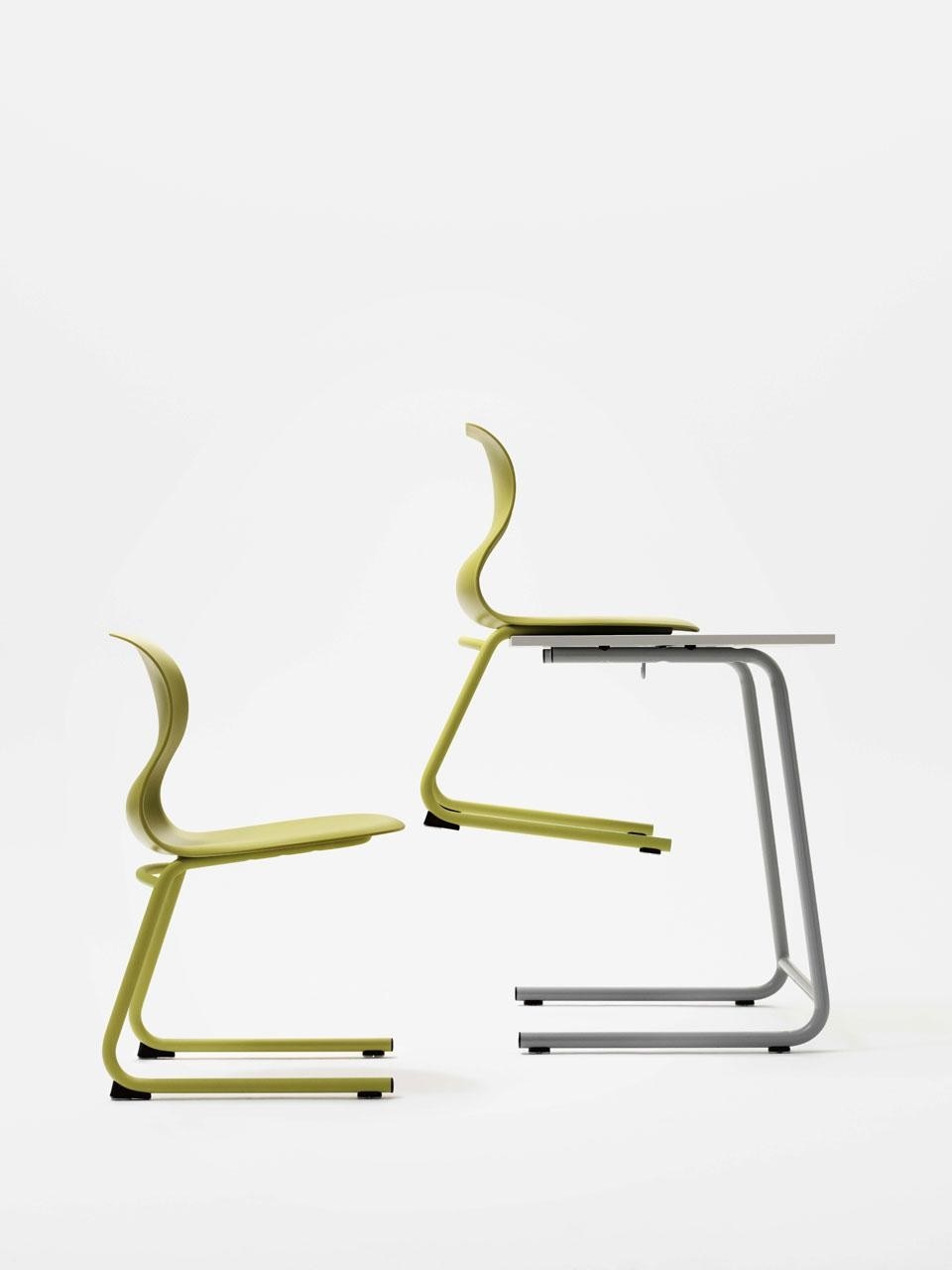
School furniture is a very national affair. Each country has not only its own norms and rules, but also its own industry producing school furniture. In Germany there are 3–4 main players splitting the pie. The situation is not at all bad for these companies, which is where the problem lies. The lack of competition hinders industry to push for innovation and thus catching up with the conclusions drawn from recent studies about the work place school.
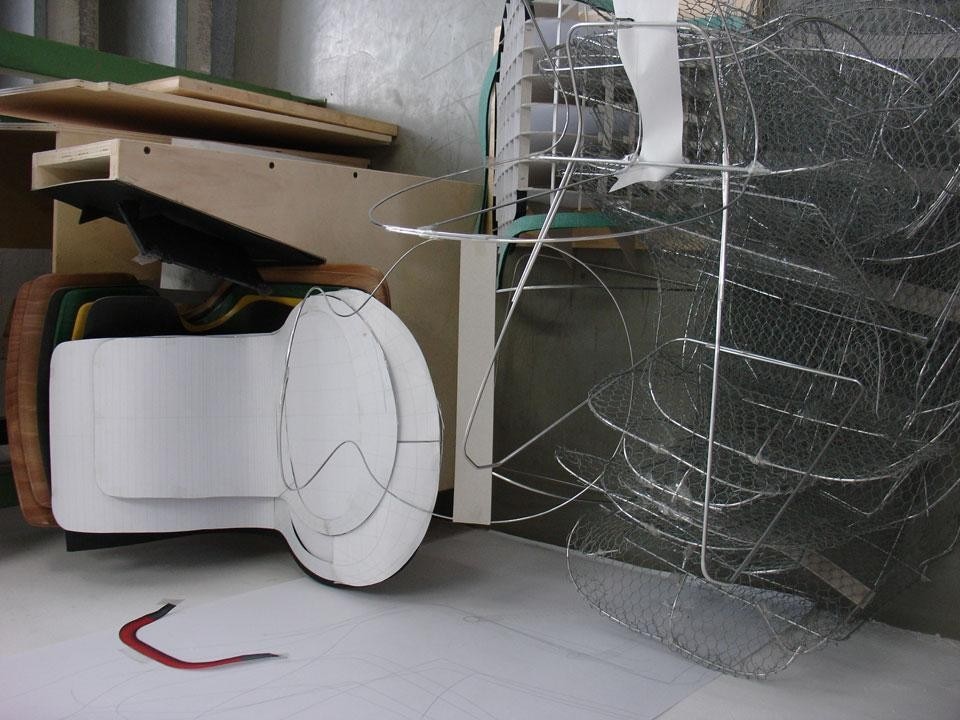
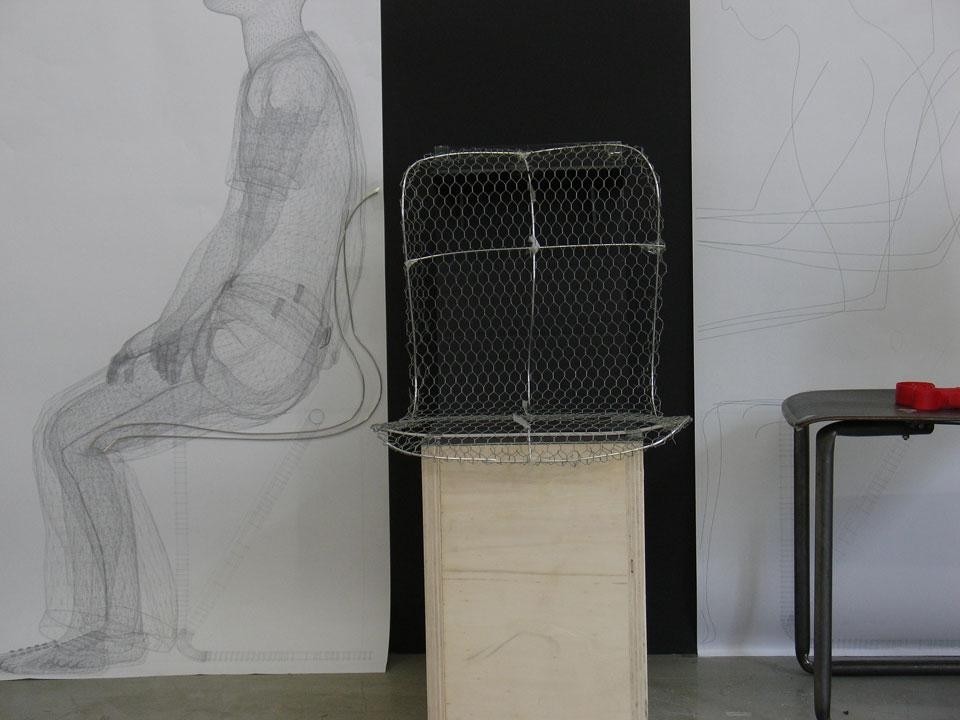