Featuring pieces from the studios of both established and emerging designers, The Aram Gallery uses this exhibition as a way to examine how designers' processes are developing to accommodate new technological advances. We offer our visitors an idea of what 3D printing is, and how it is being contemporaneously used. This exhibition is not intended as an exhaustive overview, but a cross-disciplinary pick and mix of examples.
3D printing, the summary term for Rapid Prototyping or Additive Manufacturing is a means of creating three-dimensional objects using a specifically designed printer. In place of 'ink' a continuous strand of, most commonly, polyamide or nylon is layered up to create a 3D form based on a computer drawn image. Early uses of 3D printing were for creating prototypes as the process, although costly, is much quicker than producing a handmade model. More recently, rapid prototyping technology is being used to produce 'finished', end designs.
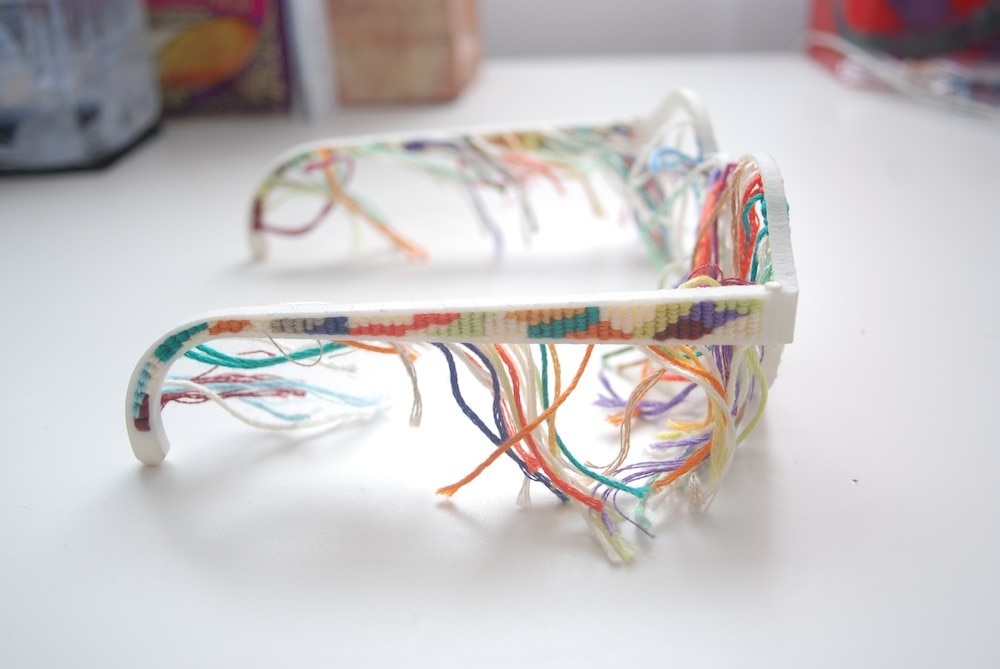
Above: Chloë McCormick and Nicholas O’Donnell-Hoare, Tapestry Spectacle, 2011. Laser Sintering/ Hand Woven Tapestry, 10 Hours.
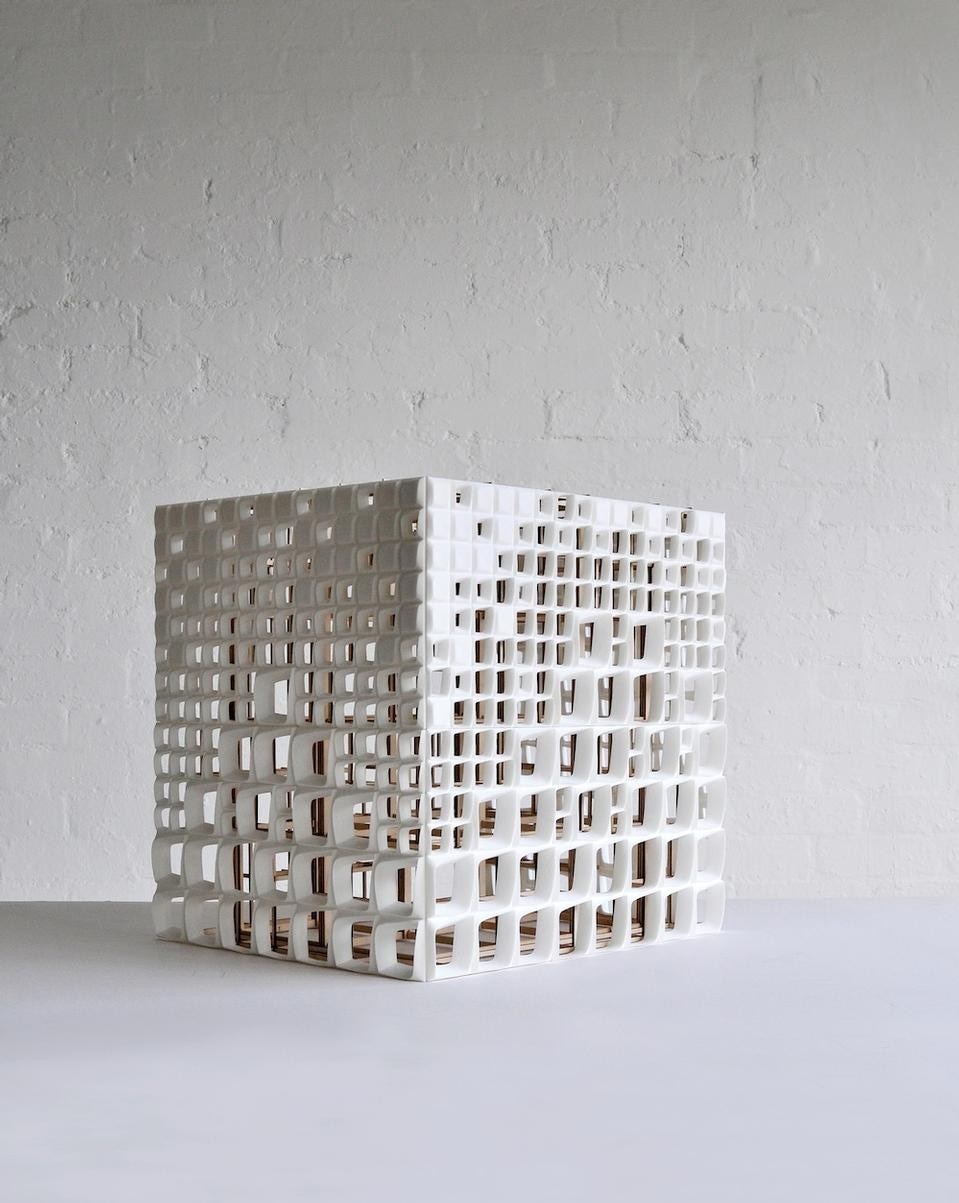
13 January–25 February 2012
The Aram Gallery
110 Drury Lane
Covent Garden
London WC2B 5SG
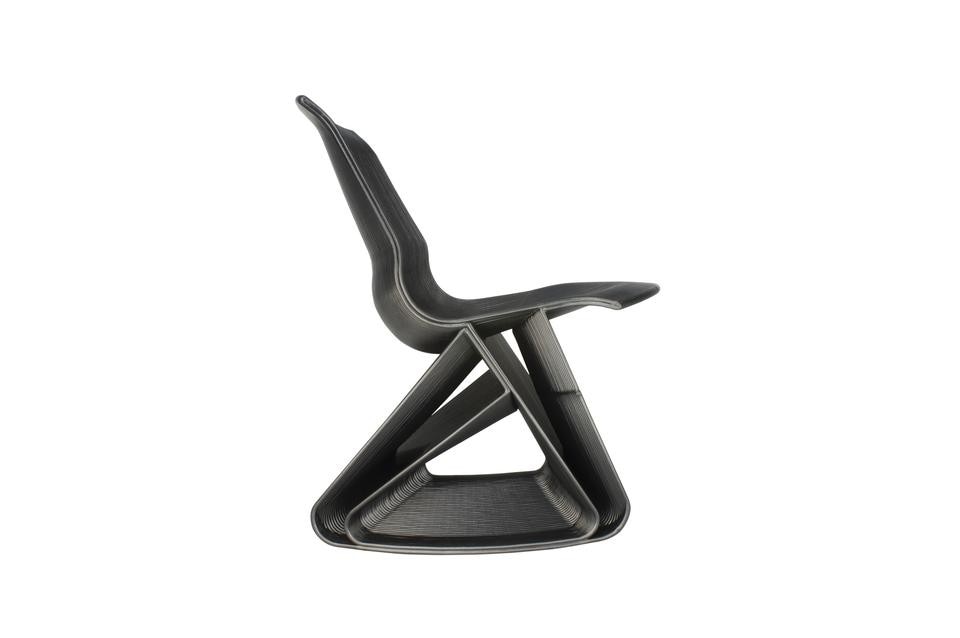
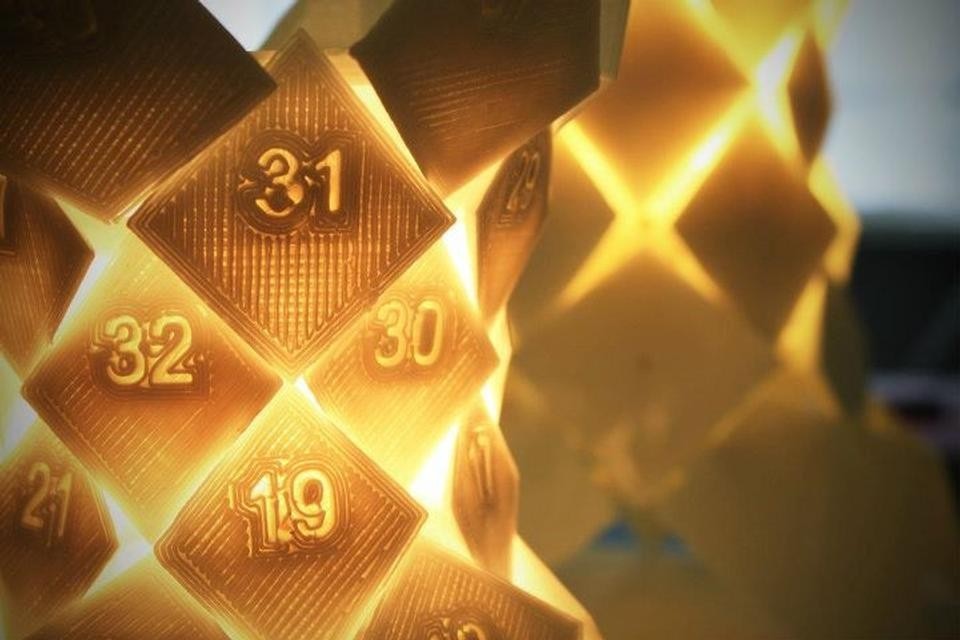
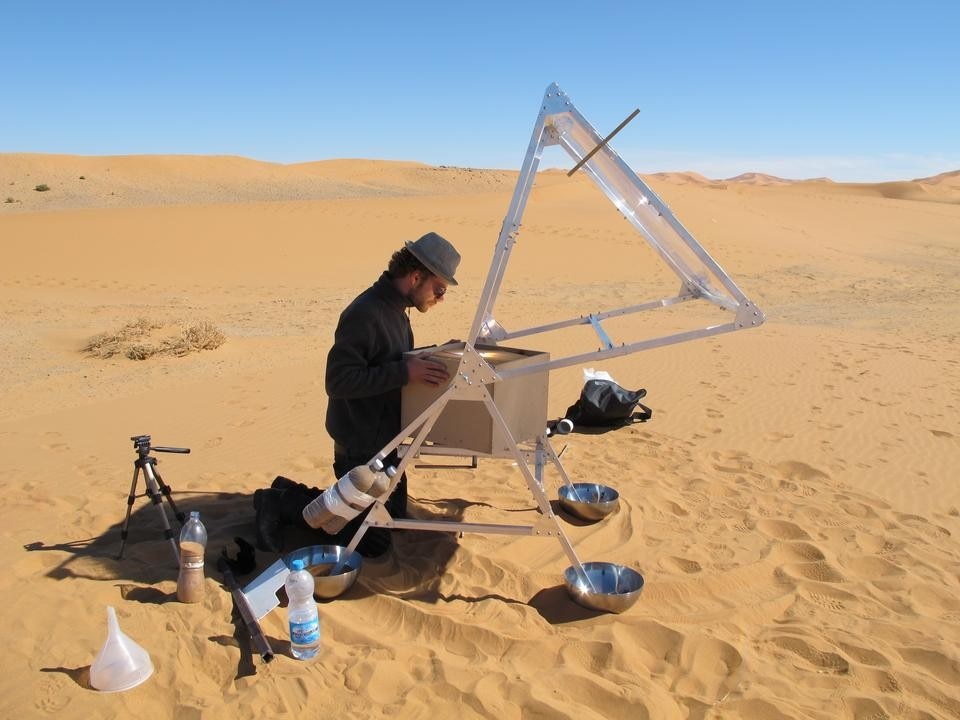
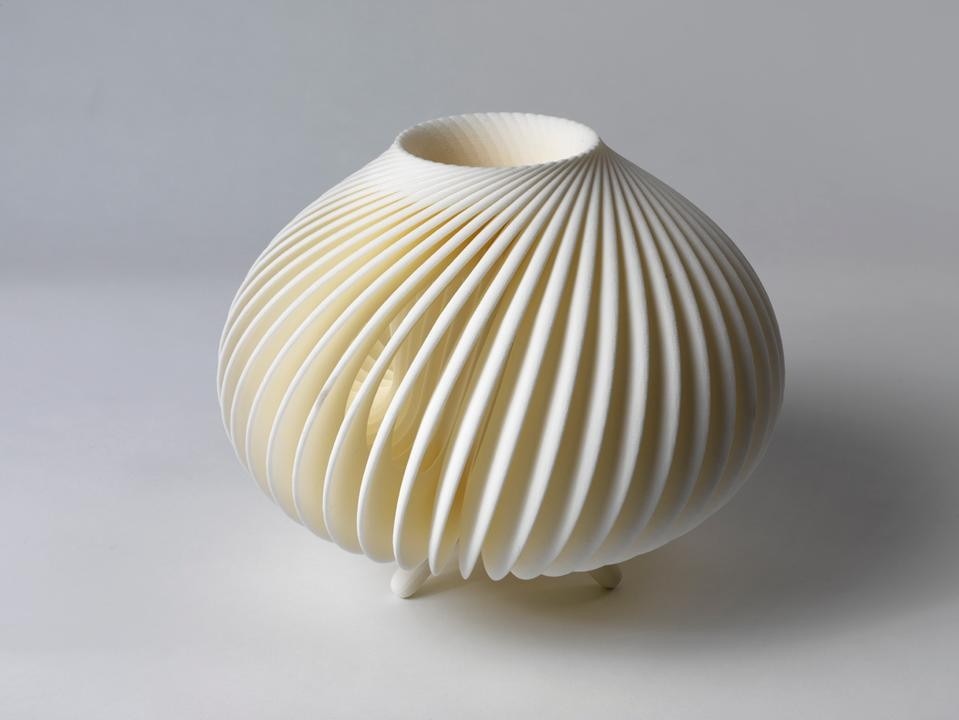